Projects
Projects
We take pride in our work — and we're confident it shows.
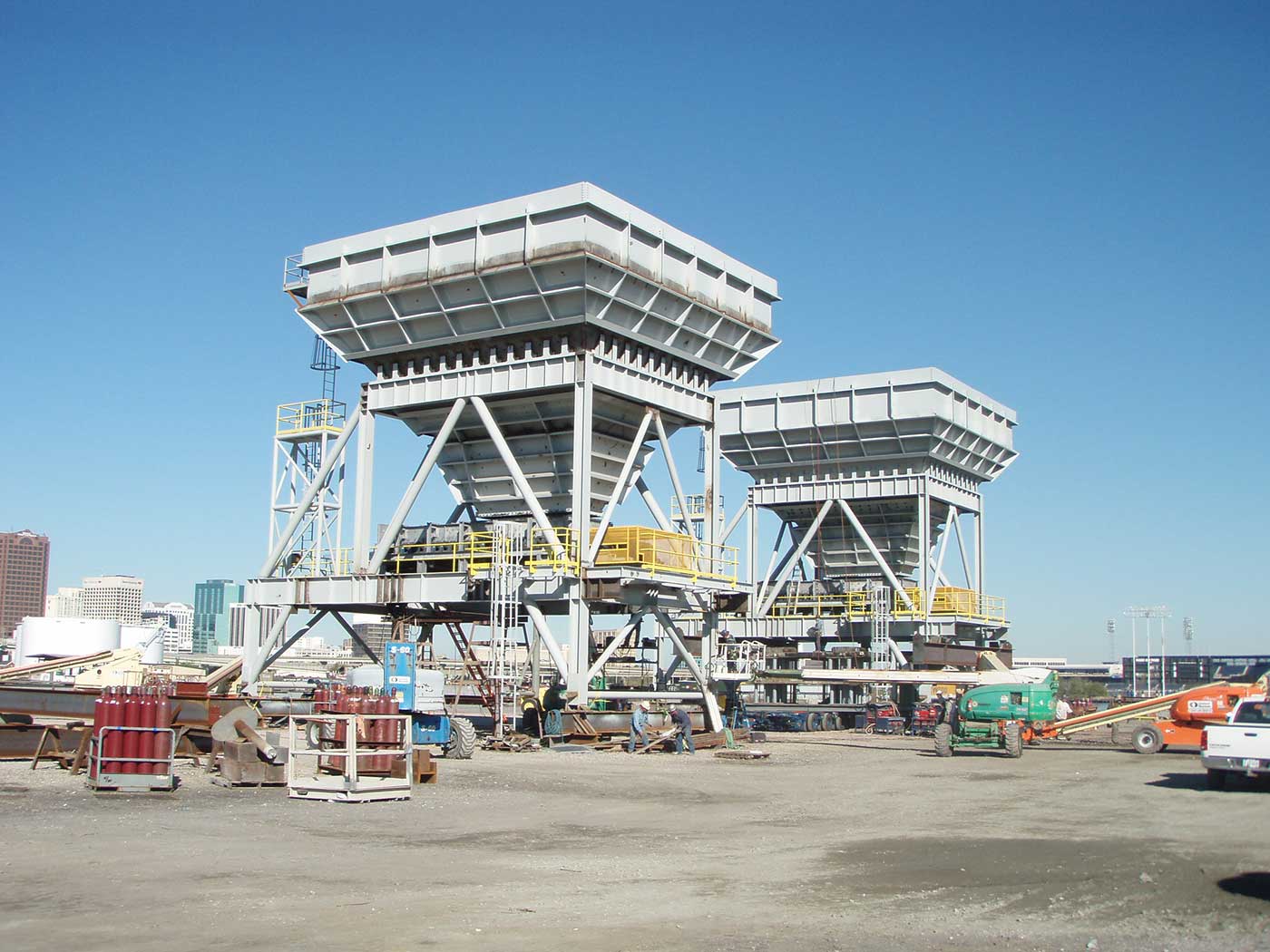
Kinder Morgan Coal Hoppers
This job consisted of fabricating two (2) 240-ton independently traveling coal hoppers that work in unison with two (2) 360 ton Gotwald cranes and an air suspended conveyor system. Quality Assurance inspectors used a variety of advanced, non-destructive test (NDT) procedures to ensure that the workmanship and materials met the highest standards set forth. These units were delivered and positioned without incident and well within dimensional tolerances. The total project weight was roughly 480 tons.
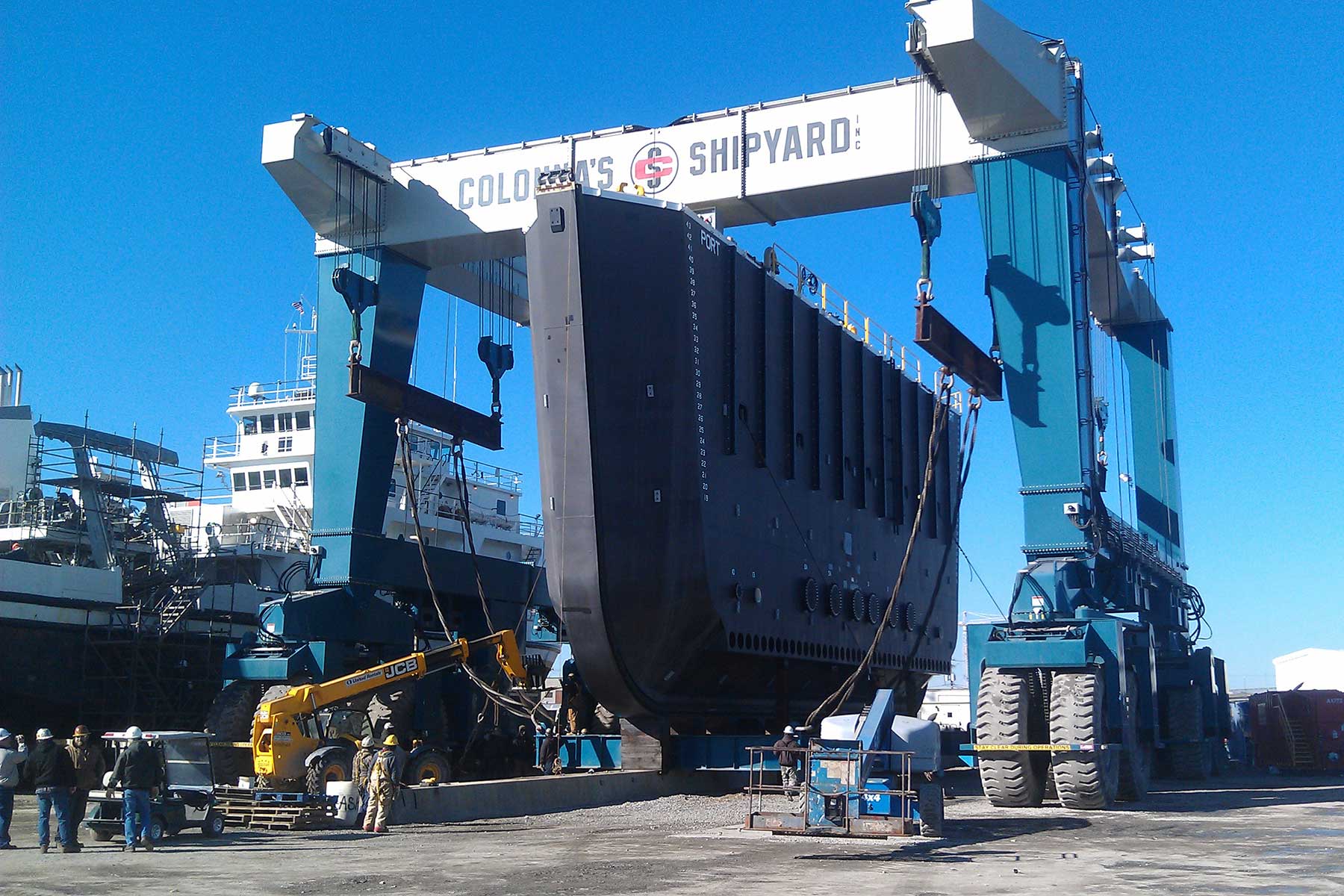
Norfolk Naval Shipyard Caisson #3
Steel America fabricated the replacement drydock caisson gate for graving dock #3. This gate is 113’-3 1/2” long by 44’-7 5/16” tall by 16’-0” wide and consists of over 440 tons of steel. This was a complete turnkey package including all piping systems, valves and pumps, all electrical work, HVAC, mooring equipment, seals, and outfitting items.
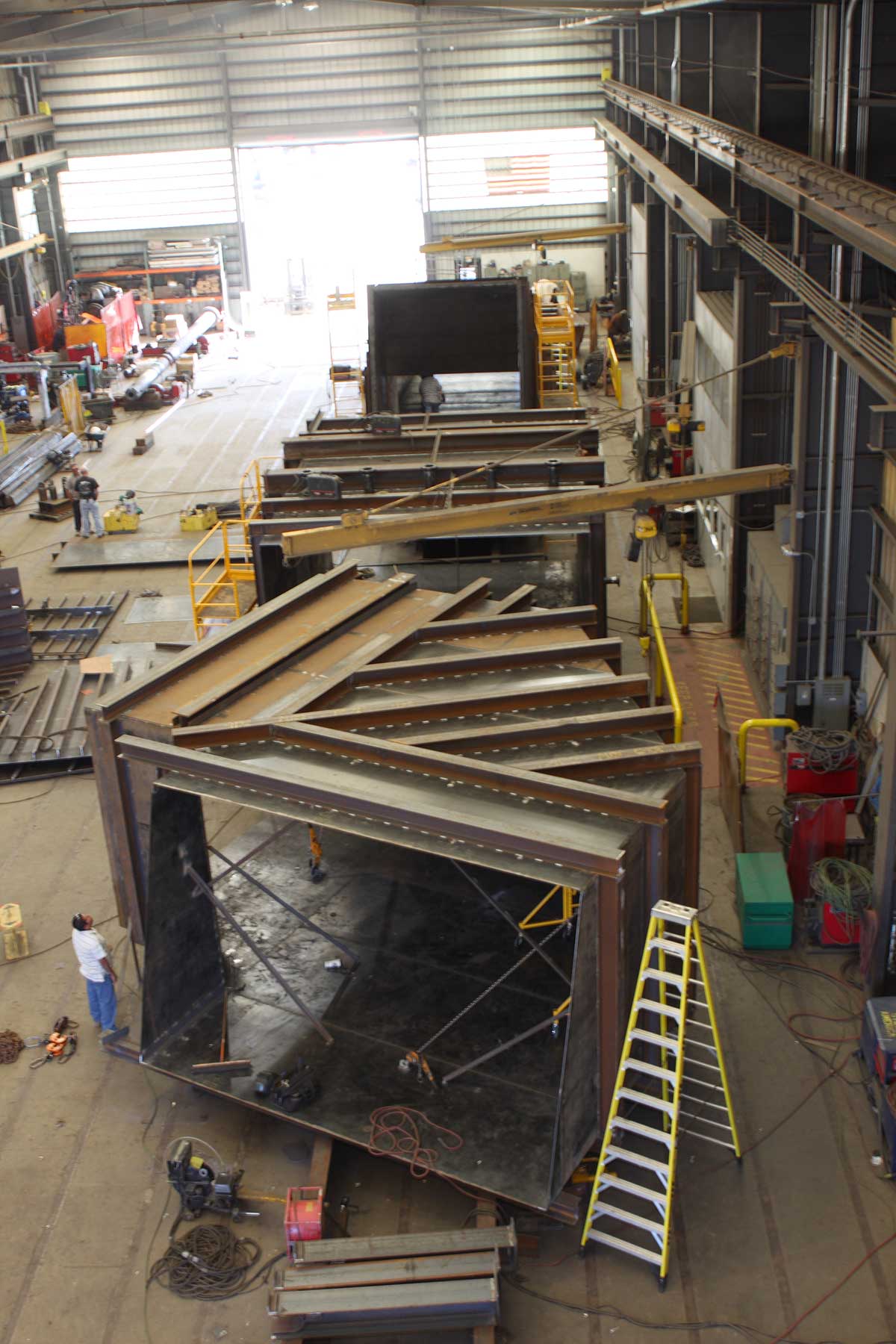
Chesterfield Ductwork
This project encompassed detailing, fabricating, and delivering two and a half (2 1/2) million pounds of new ductwork for Units 3, 4, and 5 at the Chesterfield Power Station operated by Dominion Energy. This site uses a flue gas desulfurization system for which Steel America fabricated fifty-six (56) individual ductwork units ranging from five (5) to eighty (80) short tons and up to 45’-0” square. The units were delivered to the customer via fifteen (15) barges.
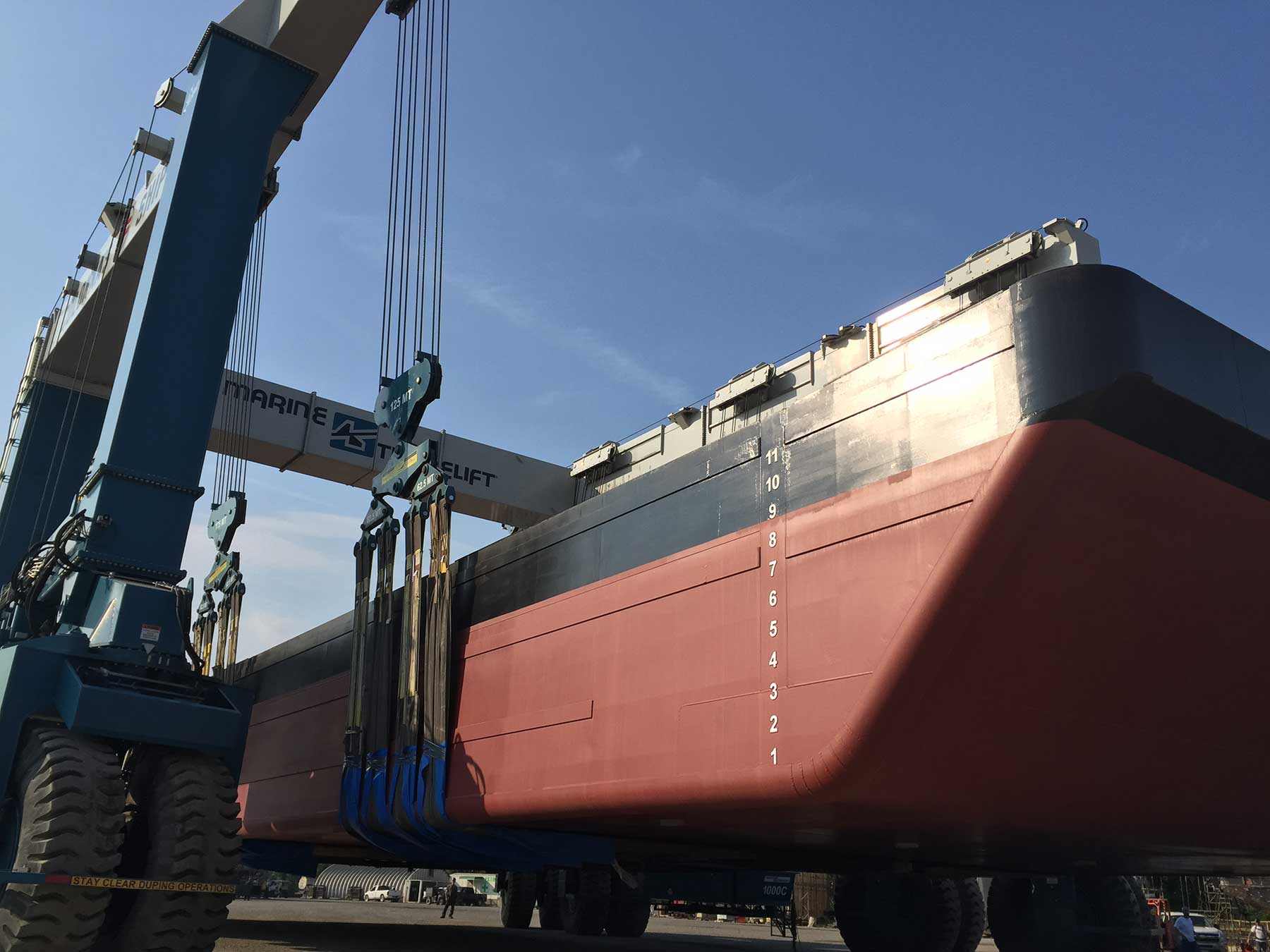
Container Barge
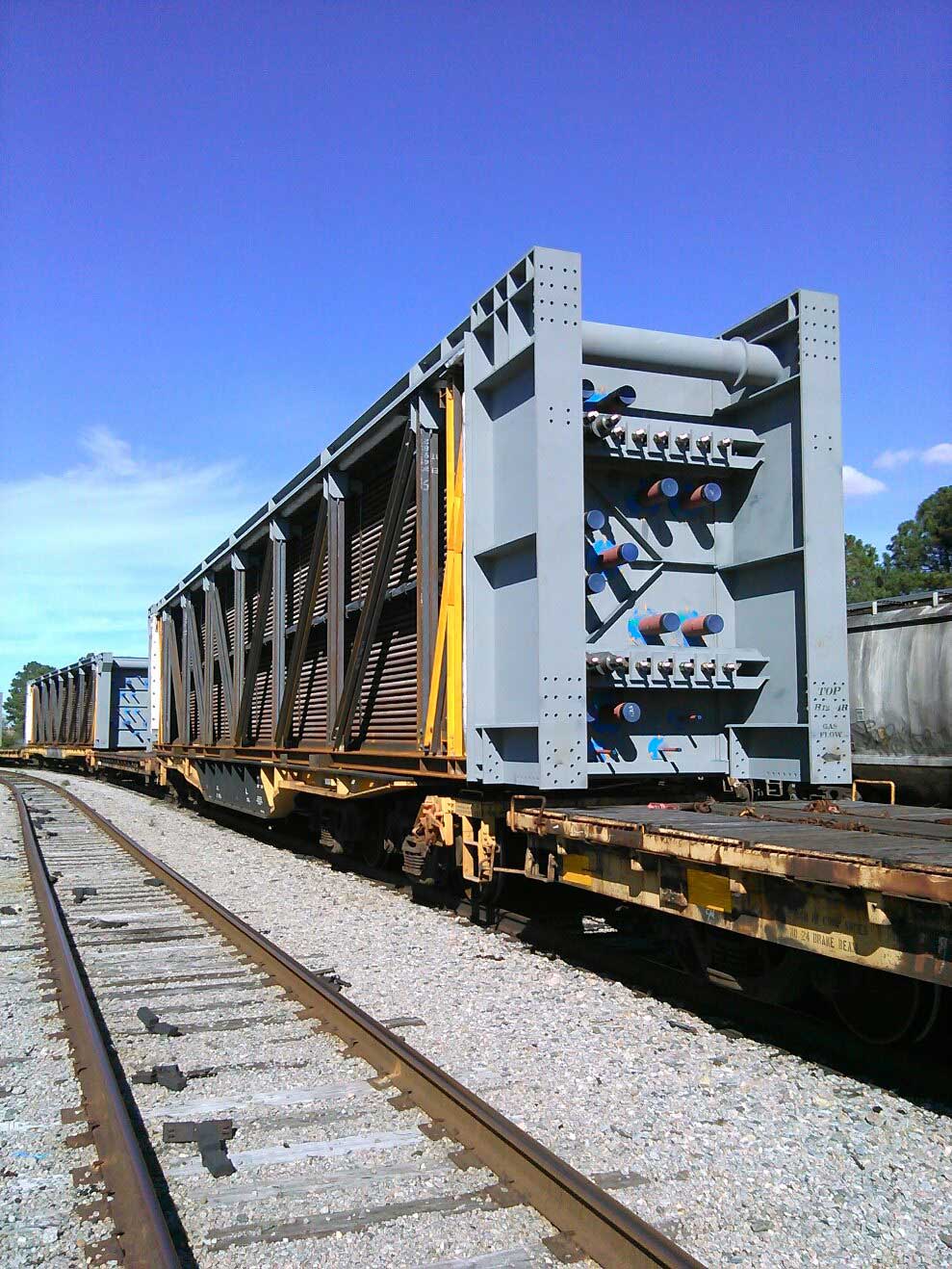
Panda Stonewall
Steel America performed an emergency repair to a main support column on a project, initially fabricated overseas, being shipped to the U.S. via the Lambert’s Point docks in Norfolk. Upon completion of the first phase of the repair, Steel America was issued 5 additional phases of work on this project. In total, the Steel America on-site fabrication team installed over 1,500 linear feet of gas baffles and installed 432 expansion bellows on 24 boiler boxes.
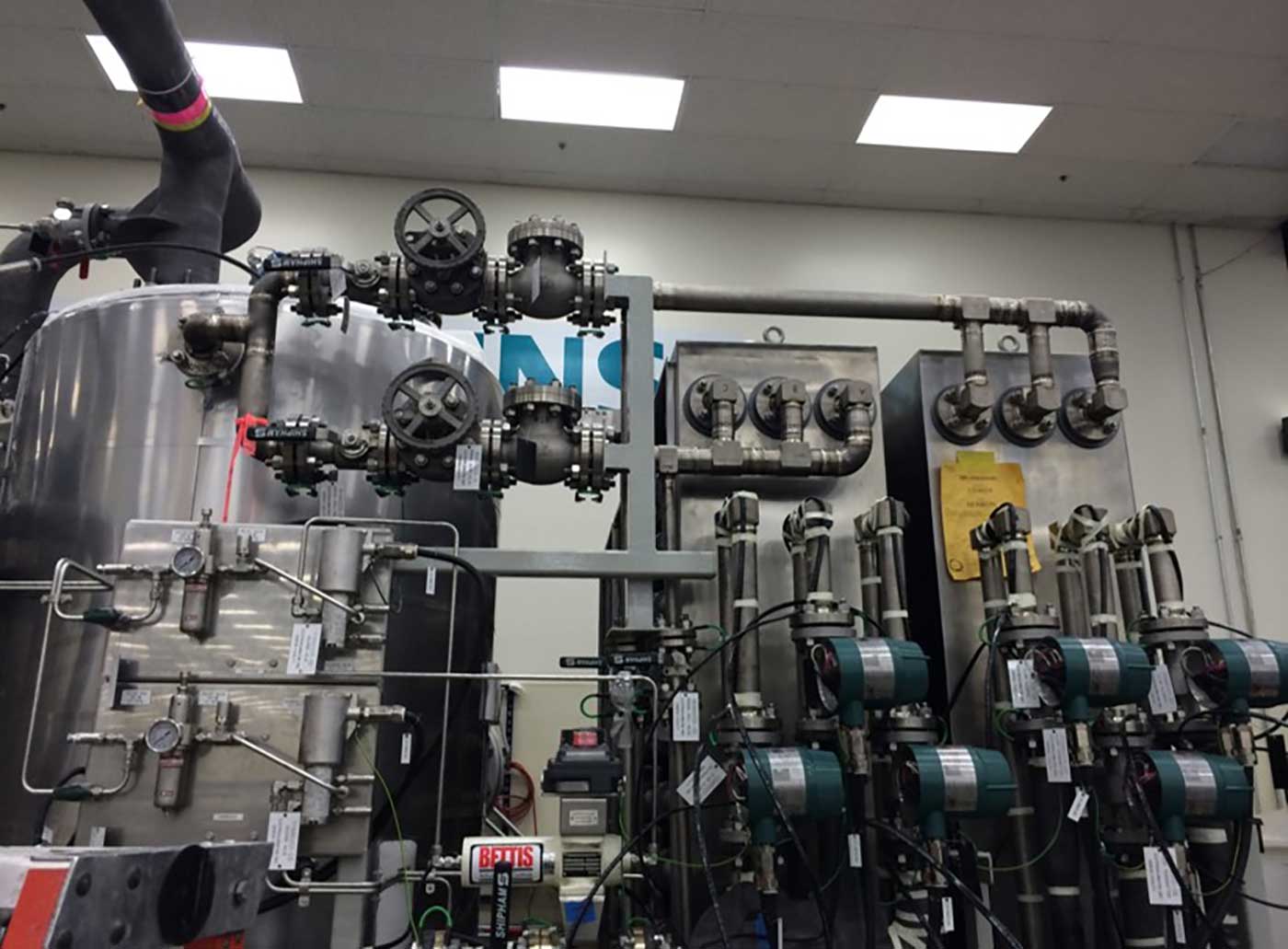
Titanium Piping
Fabricated a 35’x107’ rectangular wind tunnel, weighing roughly 77-tons, for a leading aeronautical research university. The wind tunnel has two round-to-square transitions throughout the 250’ path of ductwork.
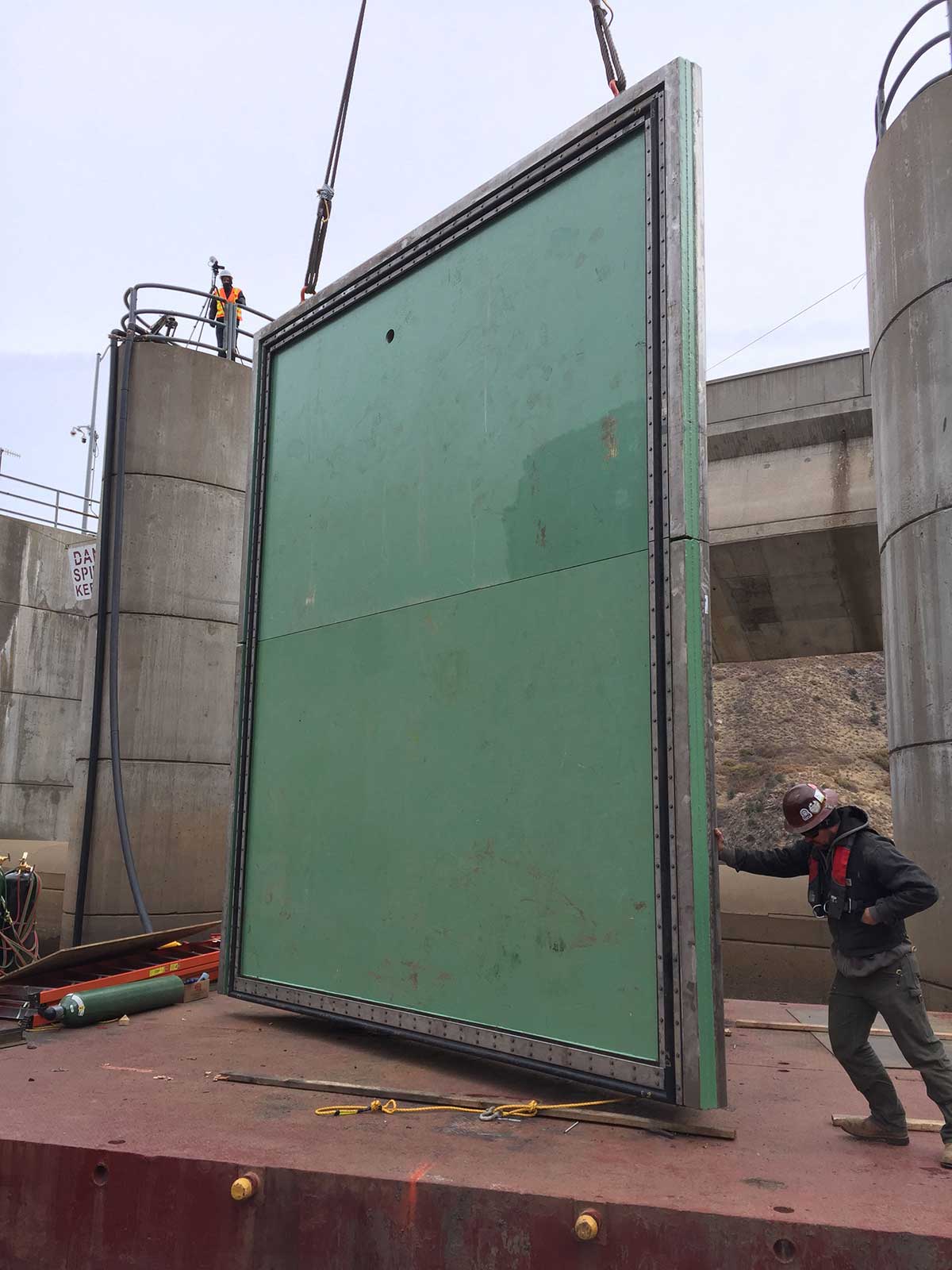
Denver Water Bulkhead
The project consisted of detail design, fabrication, welding, machining, assembly, and painting of a 14’-6” wide x 18’-2” tall steel and stainless steel bulkhead gate assembly. The gate was fabricated in two sections with bolted connections for ease of transportation. After all welding was completed, each section was sub-harmonic vibratory stress relieved.
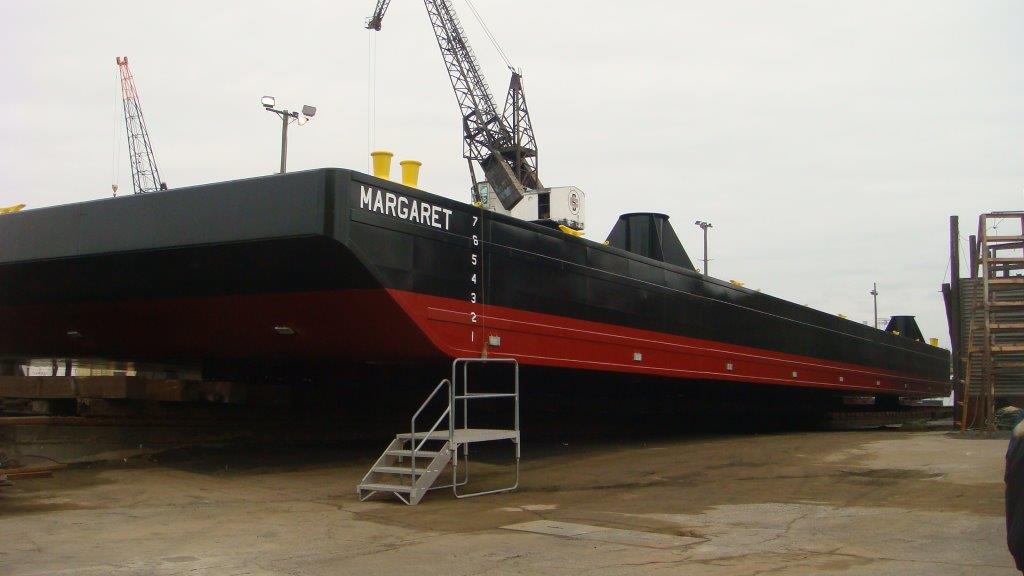
Barge “Margaret”
This project required the construction of an ABS Classed, Unrestricted, Oceangoing 160’-0” x 54’-0” x 8’-0” deck barge from modular and panel construction. This barge and kit was the third barge of this type. The barge was transported and launched from Steel America’s West Yard utilizing a 1,000 MT Travelift.
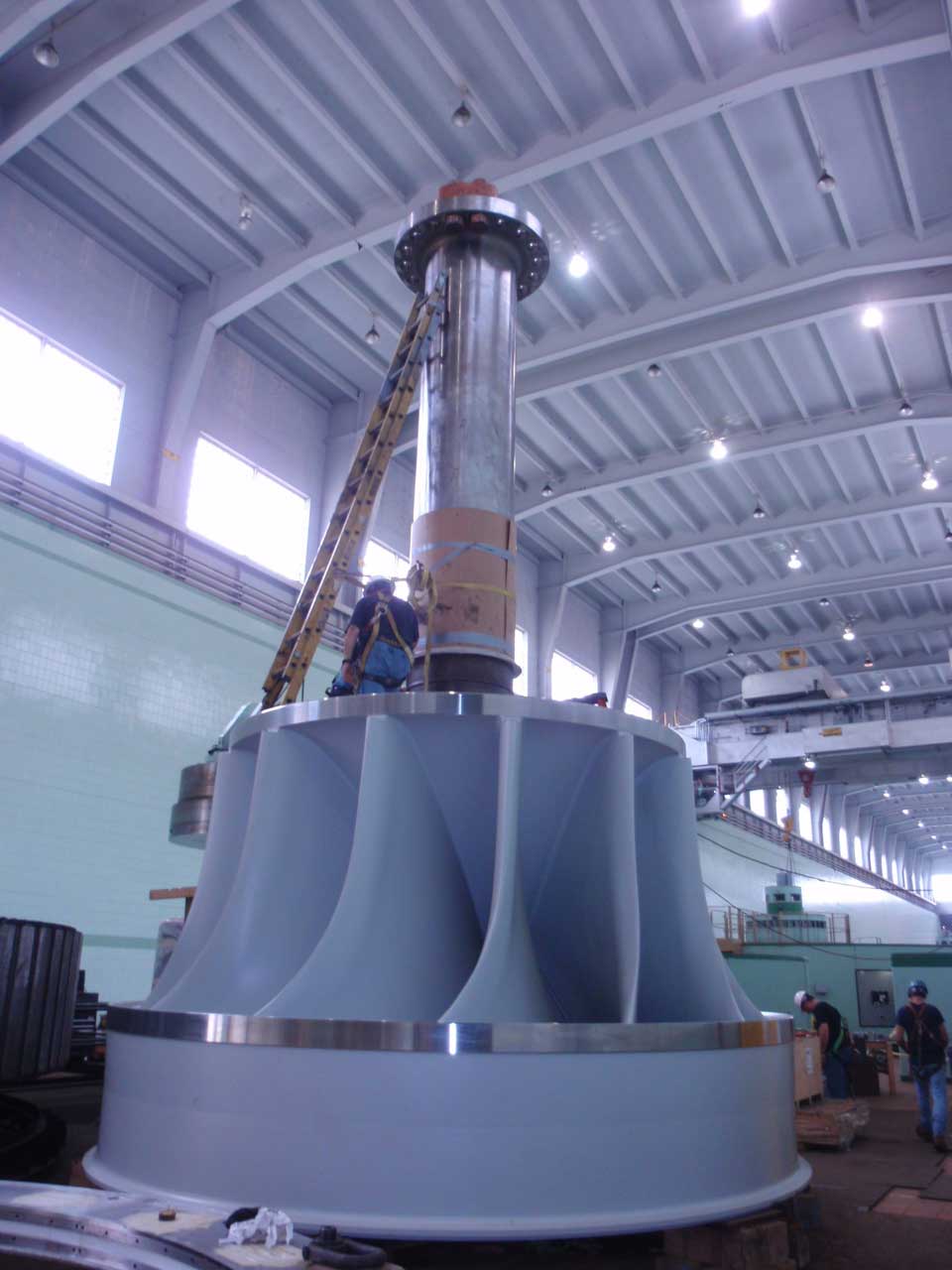
John Kerr Dam
Steel America was contracted by General Electric to perform repairs on five units in the John H. Kerr Hydroelectric Dam through a service contract. Each unit consisted of twenty-four (24) wicket gates and one (1) turbine shaft. Steel America was required to service 2 units per year with the last unit serviced in 2010 as per the customer’s schedule. Repairs to gates included sandblasting, painting, machining, welding, straightening, and NDT/inspection.
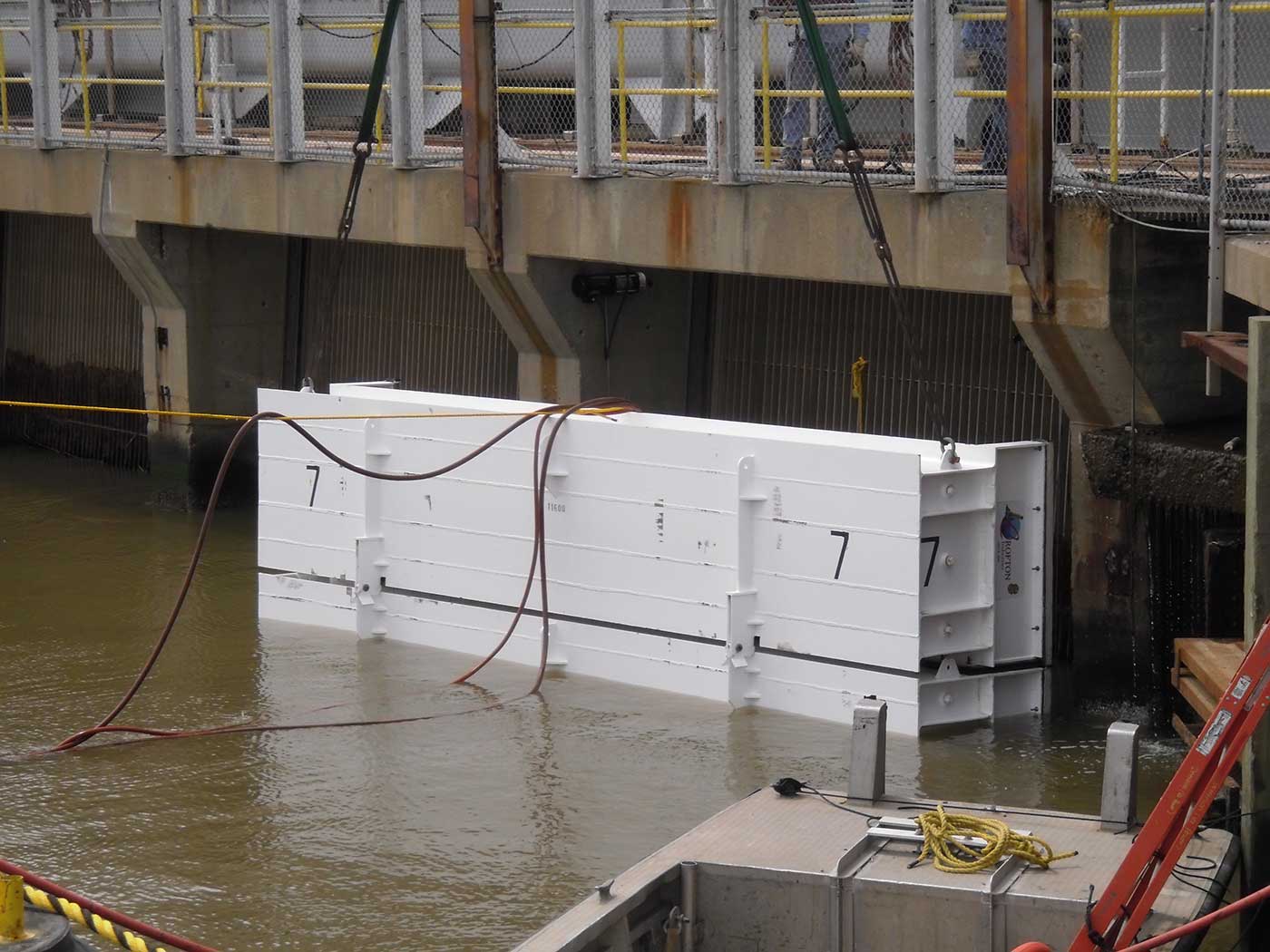
Surry Nuclear Bulkhead
This project consisted of detailing, fabricating, and painting a floating bulkhead to be used for maintenance on the gates at Dominion Surry Nuclear Power Station operated by Dominion Power. This particular floating bulkhead consisted of seven (7) individual, 23’2” wide, I-beam caissons which allowed the operator to fill the caissons individually for alignment while submerging the bulkhead. Steel America fabricated and air tested these sections while holding up to 1/16” tolerances in the shop. Weld maps and jigs were utilized to prevent distortion of these units. All interior tanks were painted, air tested to 18lbs, and purged with nitrogen prior to delivery. Steel America outfitted the units with the required j-bulb seals and test assembled the units to make sure each section was sealed in accordance with the specifications and the hinges worked correctly.
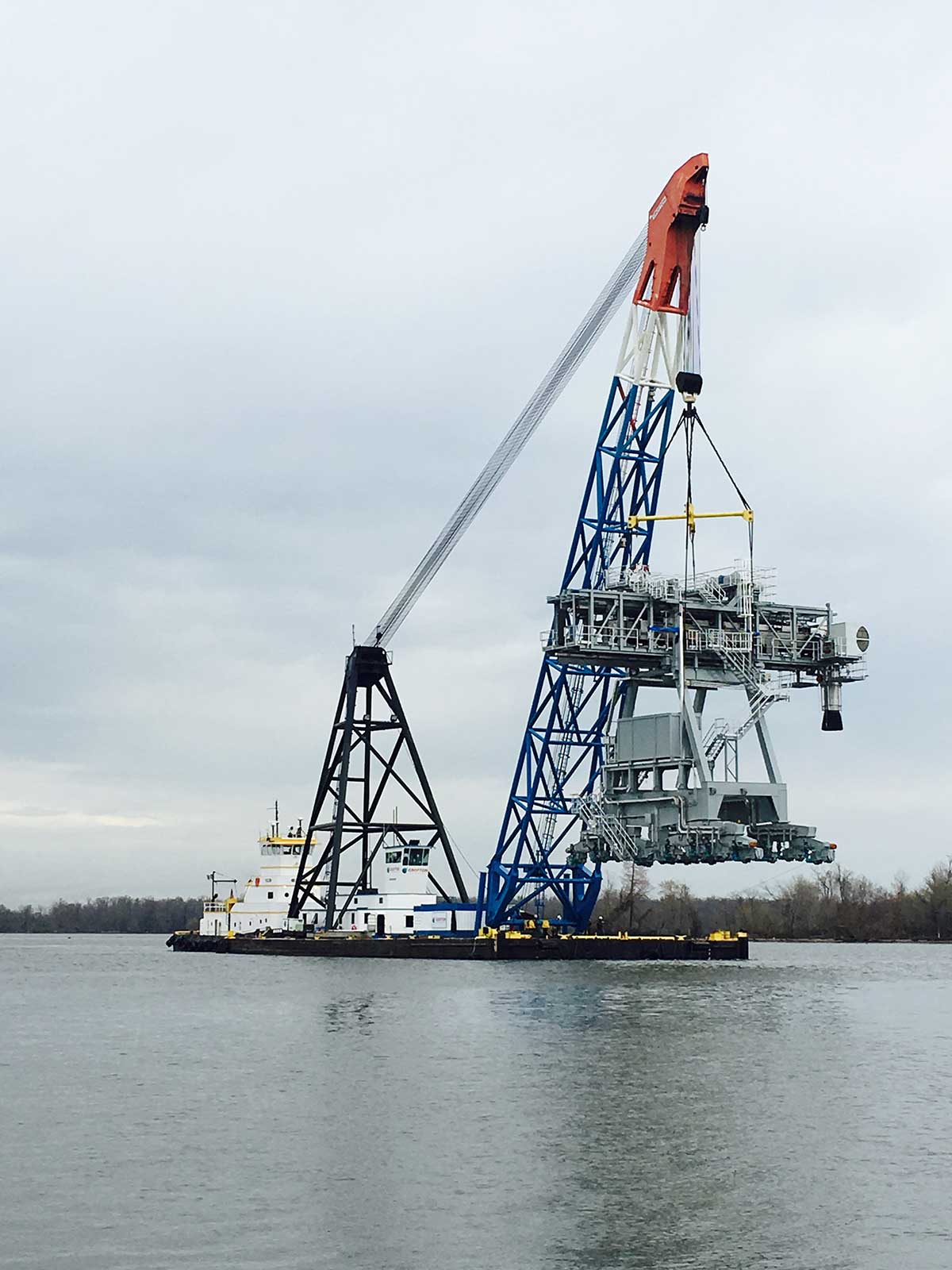
Ship Loader
The ship loader project started out as small repair job on welds. As work progressed, Steel America built the new telescoping boom, tripper and trailer and repaired nearly all parts needed to complete this project. Steel America also assembled the main gantry and catwalk systems, and shipped all by barge to Shirley Plantation for final assembly.
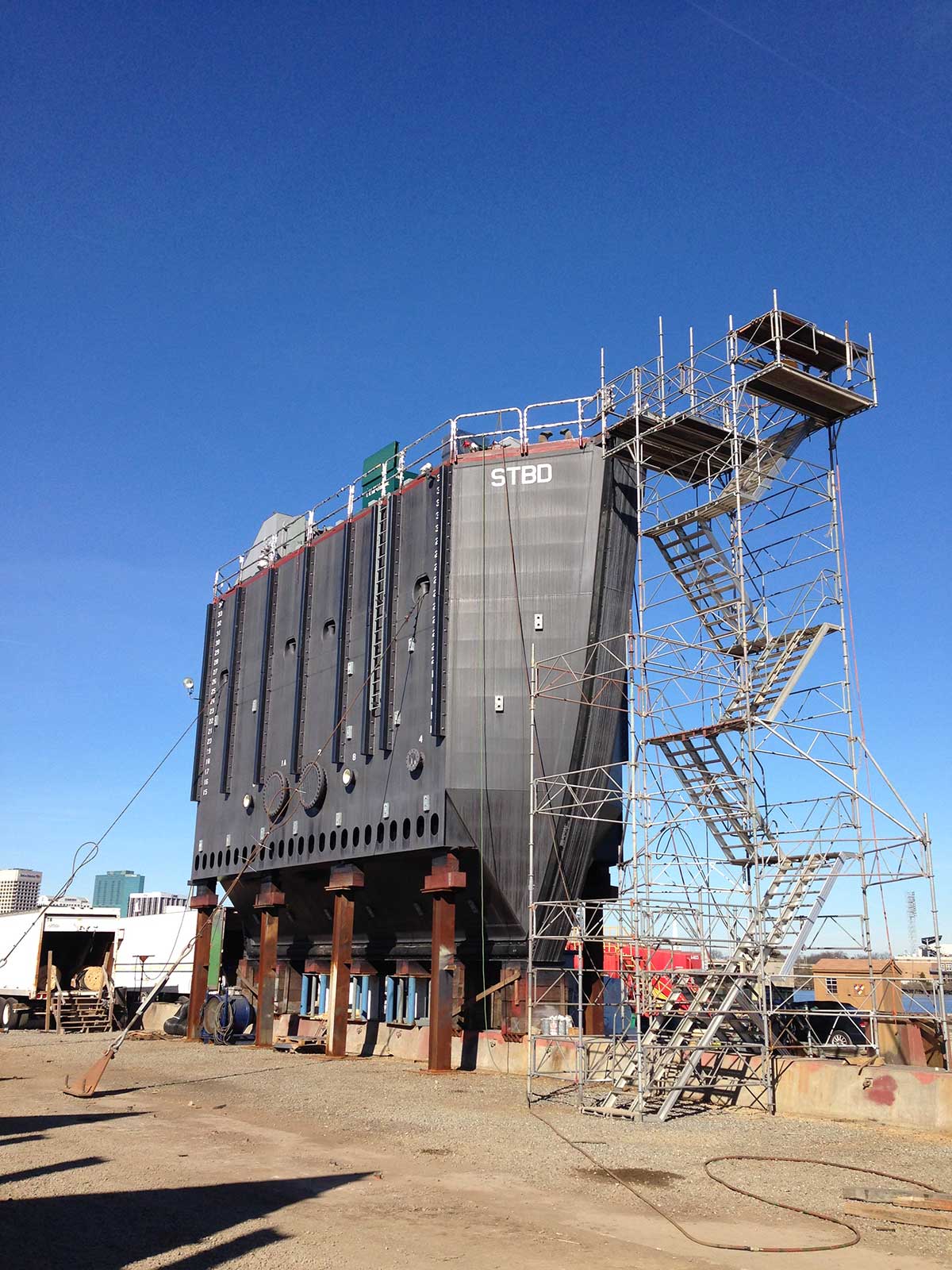
Norfolk Naval Shipyard Caisson #1
Steel America fabricated the replacement drydock caisson gate for graving dock #1. This gate is 64’-5” long by 35’-3” tall by 16’-0” wide and consists of over 318 tons of steel. This was a complete turnkey package including all piping systems, valves and pumps, all electrical work, HVAC, mooring equipment, seals, and outfitting items.
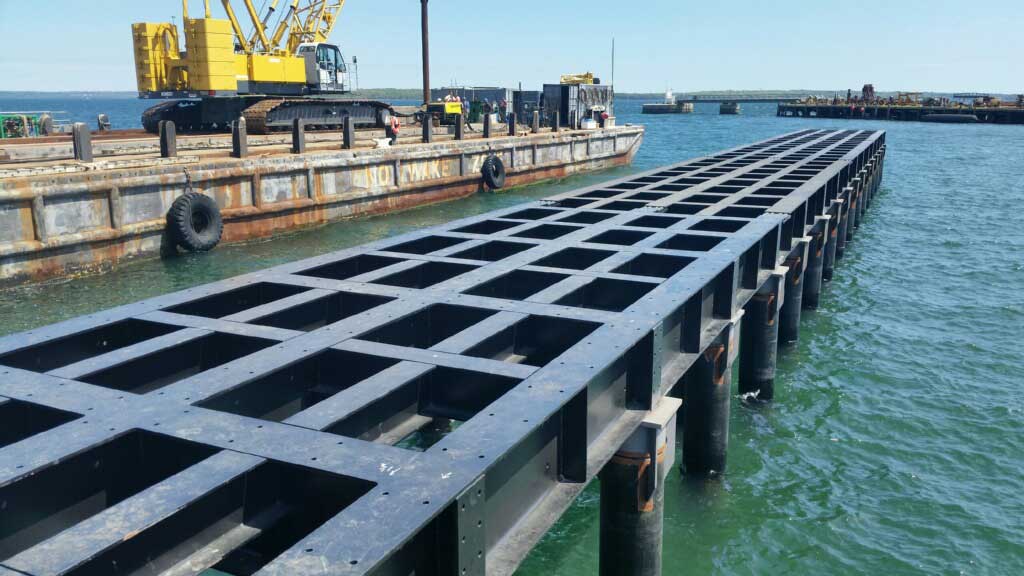
Travelift Pier
Fabrication and delivery to Rhode Island of two 160’ x 15’ steel piers with pile guides – total 315 tons of steel.
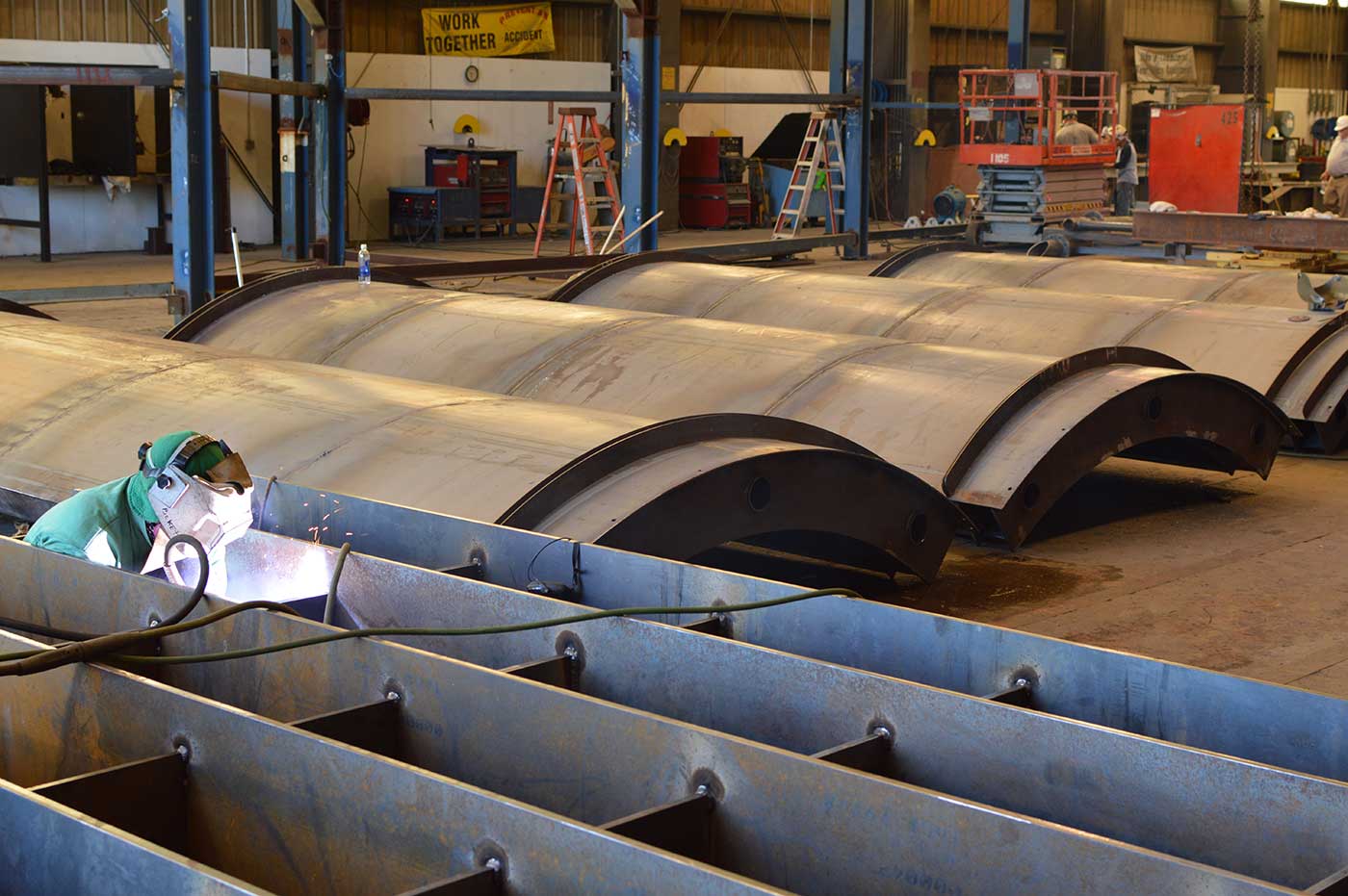
Sunoco Tainter Gates
This project was to supply (4) newly constructed Tainter Gates to replace existing gates which were in disrepair for the Prestwood Dam, located in Hartsville, S.C. This project included the detail design, fabrication, welding, machining, assembly, and galvanizing of (4) 264” x 83” fabricated steel Tainter Gates with Stainless Steel embeds, 120’ of fabricated steel Catwalk, (4) sets of fabricated Stainless Steel Stop Log Guides, and 118’ of steel trolley system. At the site the customer had to install the Stop Log guides and sills under water using dive teams so that the new Tainter Gates could be installed in a dry condition using the Stop Logs as a barrier from the reservoir.
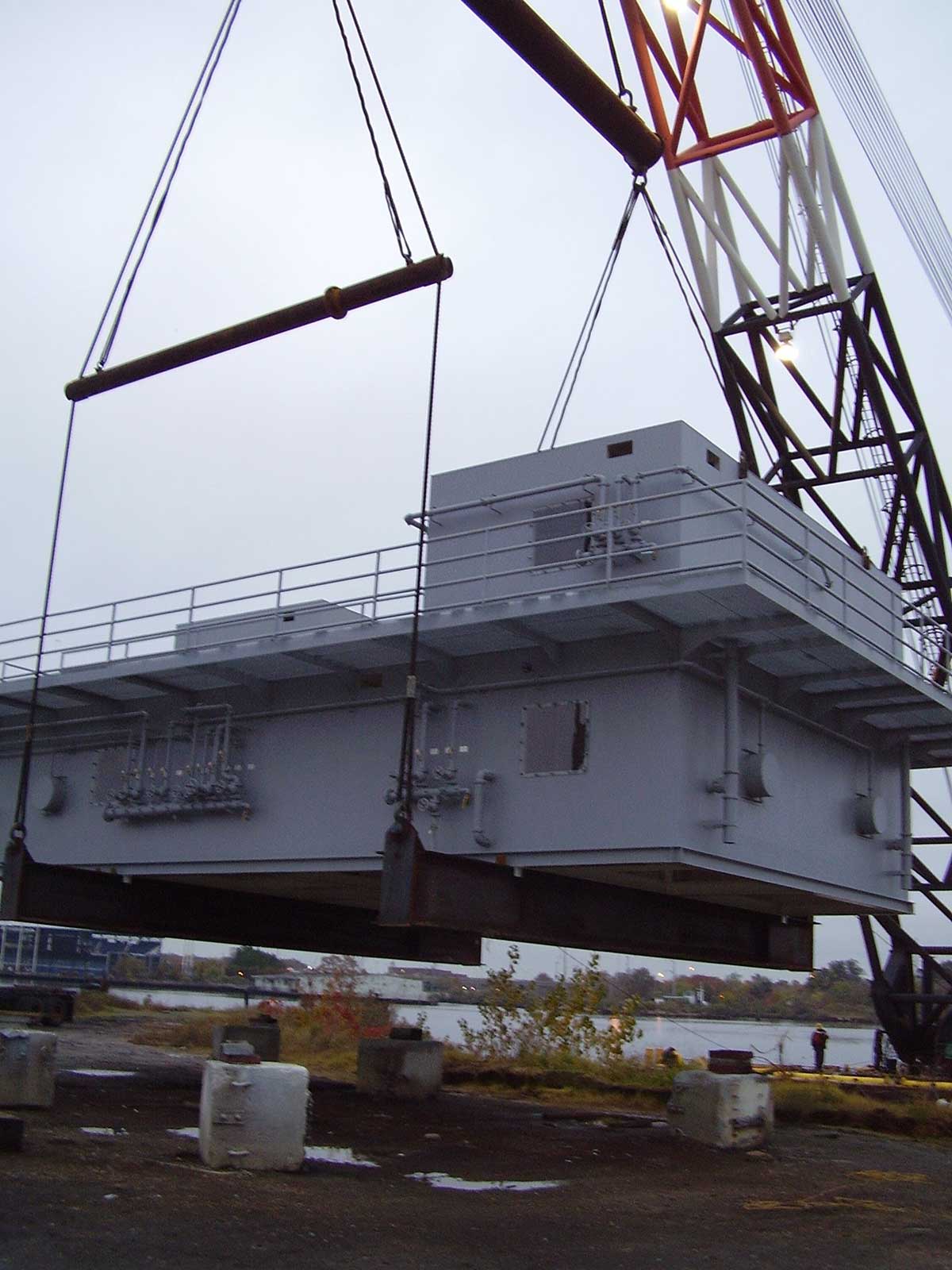
Damage Control Trainer
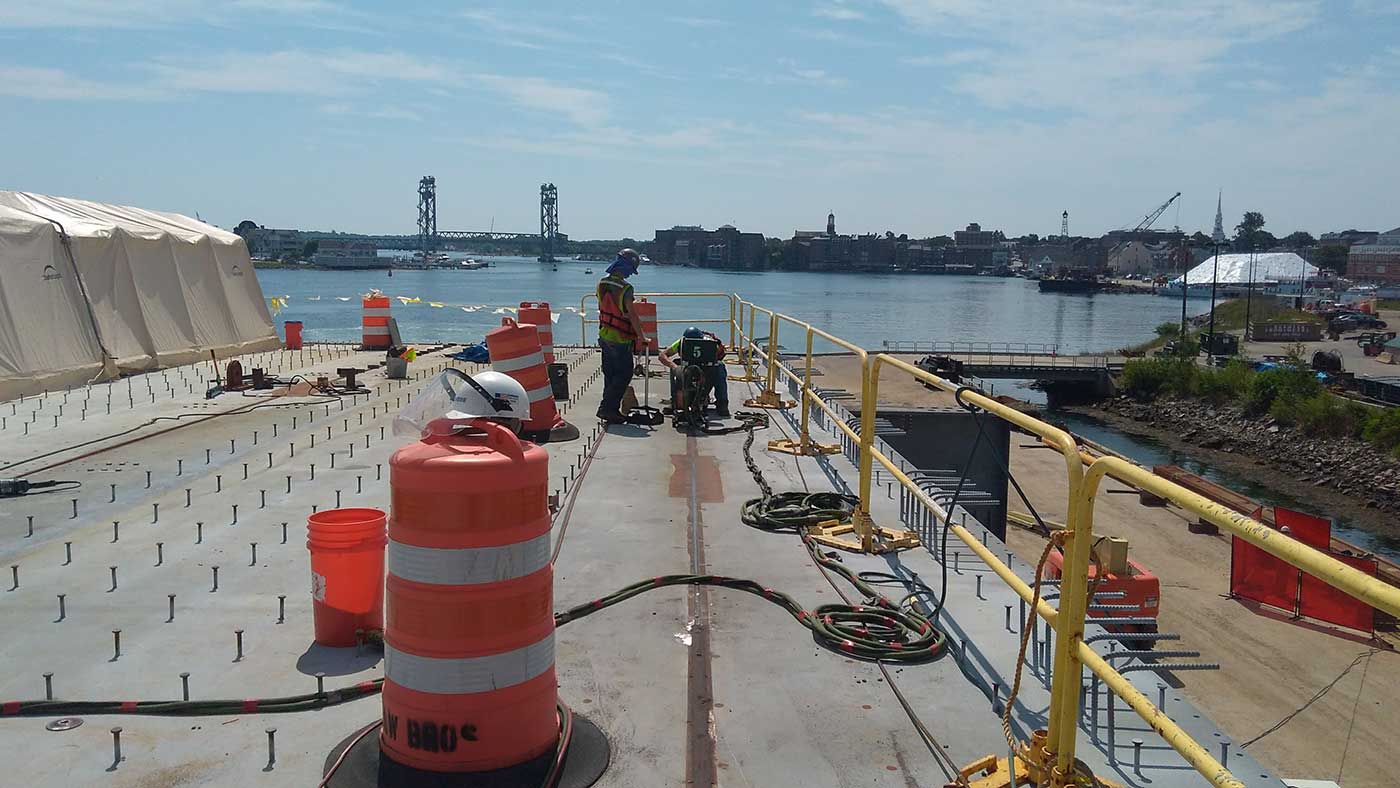
Sara Long Bridge Welding
Steel America was contracted by Cianbro to perform sub arc welding on the new Sara
Mildred Long bridge span in Portsmouth, NH. The welding was done in accordance with AWS D1.5 bridge code and federal DOT requirements. The project consists of
approximately 700 linear feet of 1” thick plate and approximately 400 linear feet of 2” thick plate. Each weld joint took roughly 20-30 passes of weld. Steel America developed an
additional safety program/procedure due to work location and to meet DOT requirements.
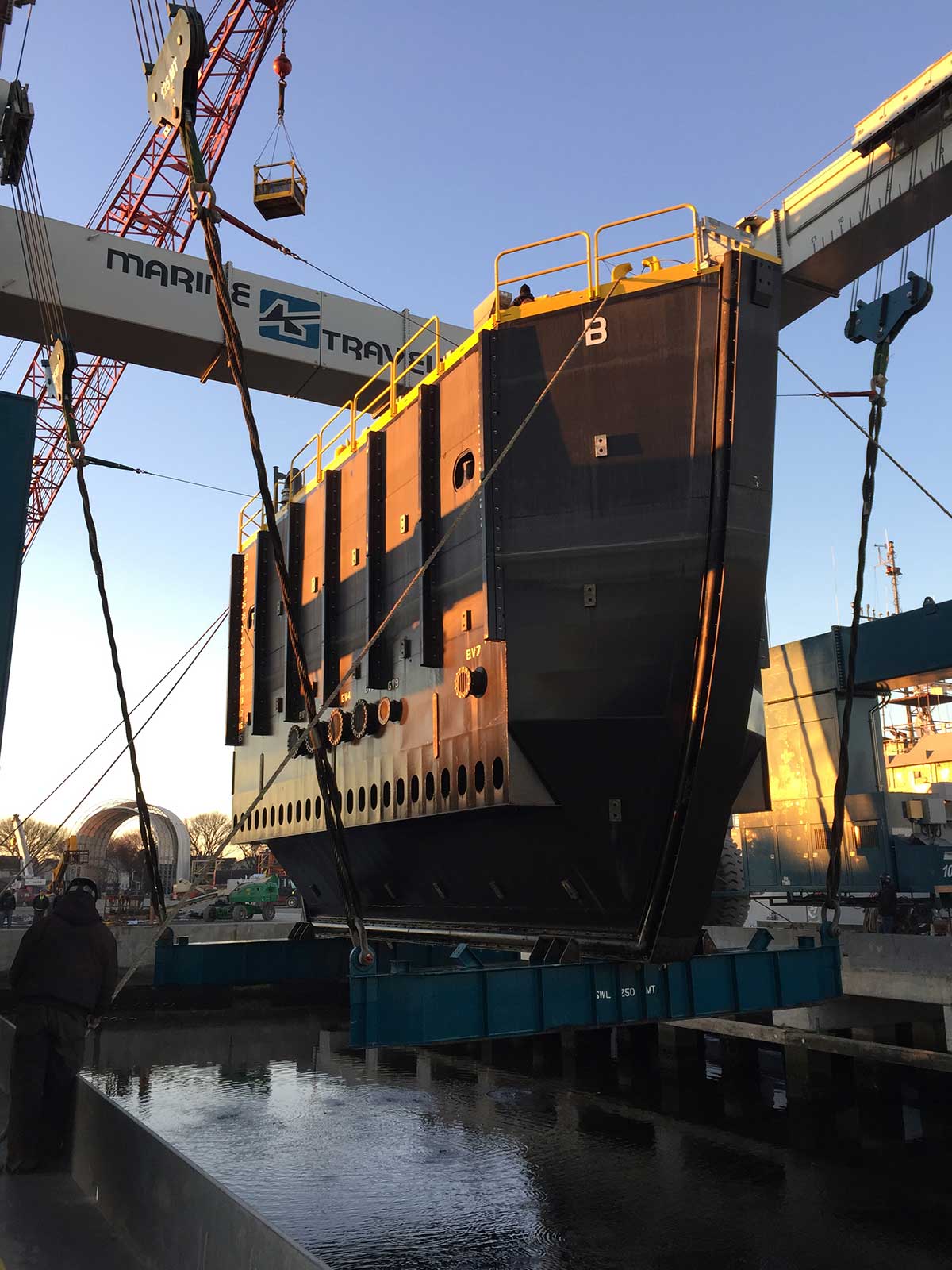
Charleston Naval Shipyard Caisson #1
This was a design-build project in which Steel America fabricated the replacement drydock caisson gate for graving dock #1. This gate is 64’-0” long by 31’-8” tall by 16’-0” wide and consists of over 296 tons of steel. This was a complete turnkey package including all piping systems, valves and pumps, all electrical work, HVAC, mooring equipment, seals, and outfitting items.
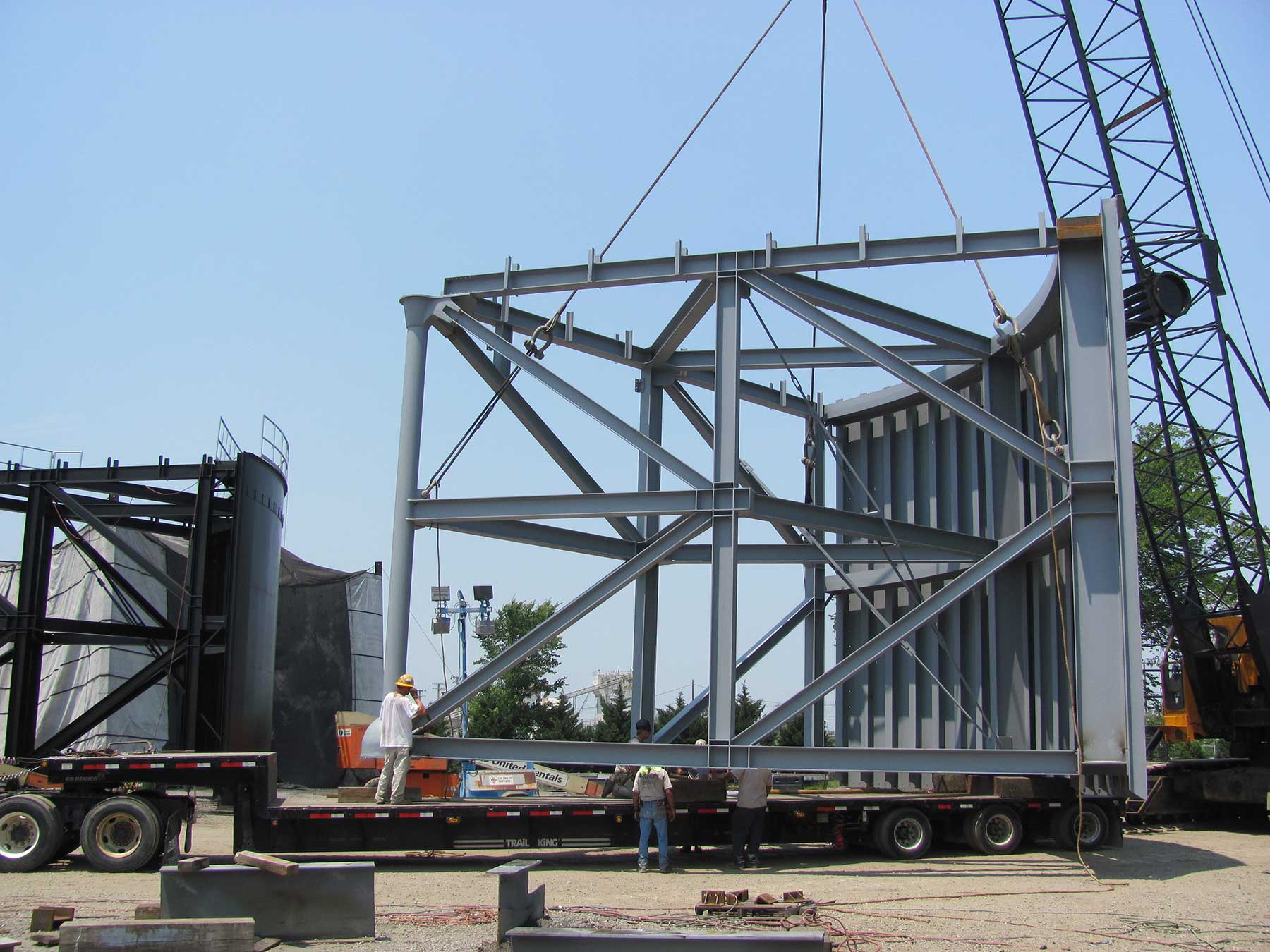
Bayou Segnette
This project is a fabricated two-sided rotating flood control gate that prevents major flooding of waterways in Bayou Segnette which is close in proximity to the Mississippi River and the City of Metairie, LA. Each gate section is 35’-0” x 35’-0” x 26’-0”. The gate sections were loaded at Steel America using a 1,000 MT Travelift onto an ocean-going barge.
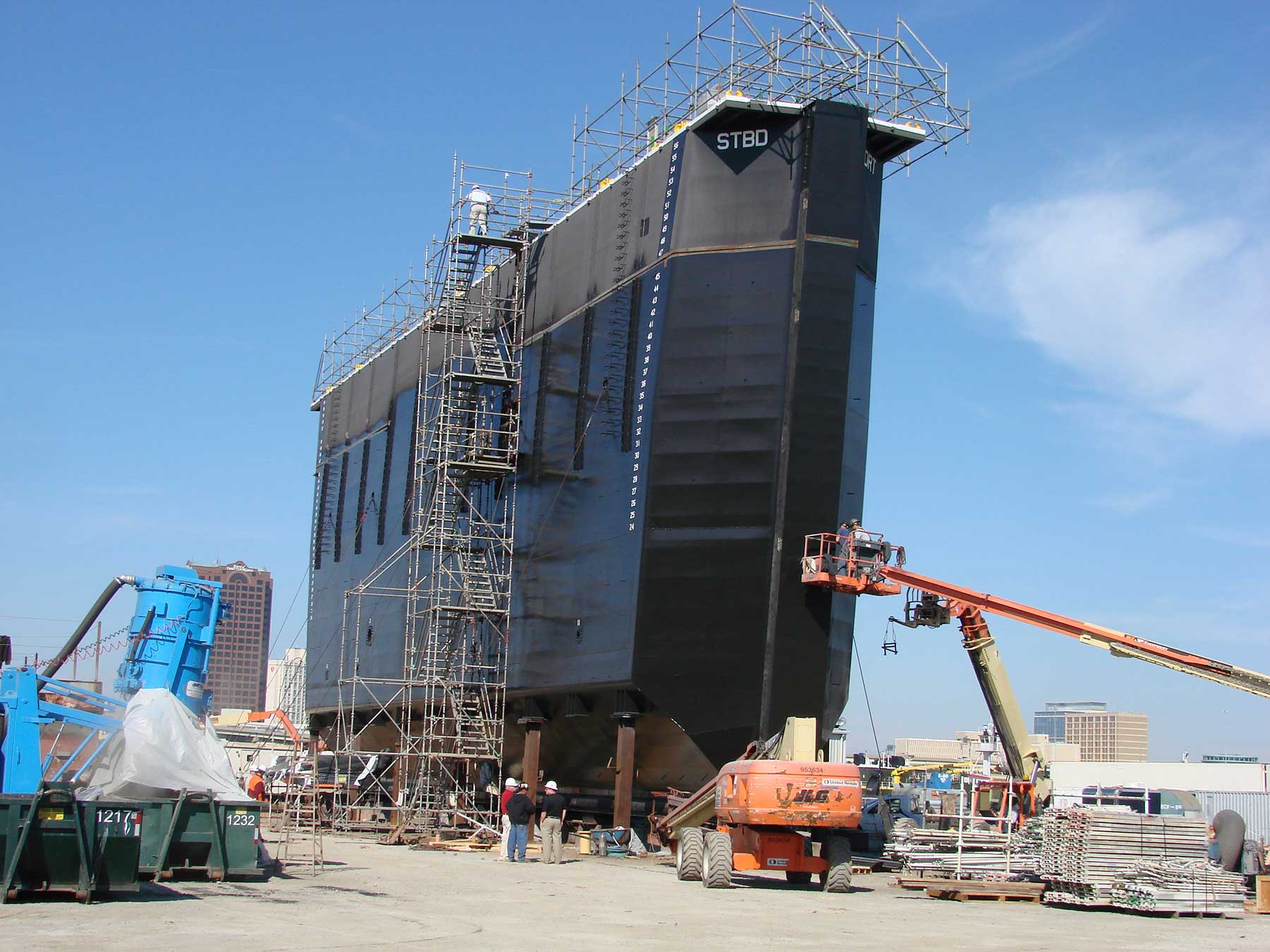
Naval Station Norfolk Caisson #8
Steel America fabricated the replacement drydock caisson gate for the Aircraft Carrier graving dock #8. This gate is 158’-0” long by 57’-0” tall by 20’-0” wide and consists of over 920 tons of steel.
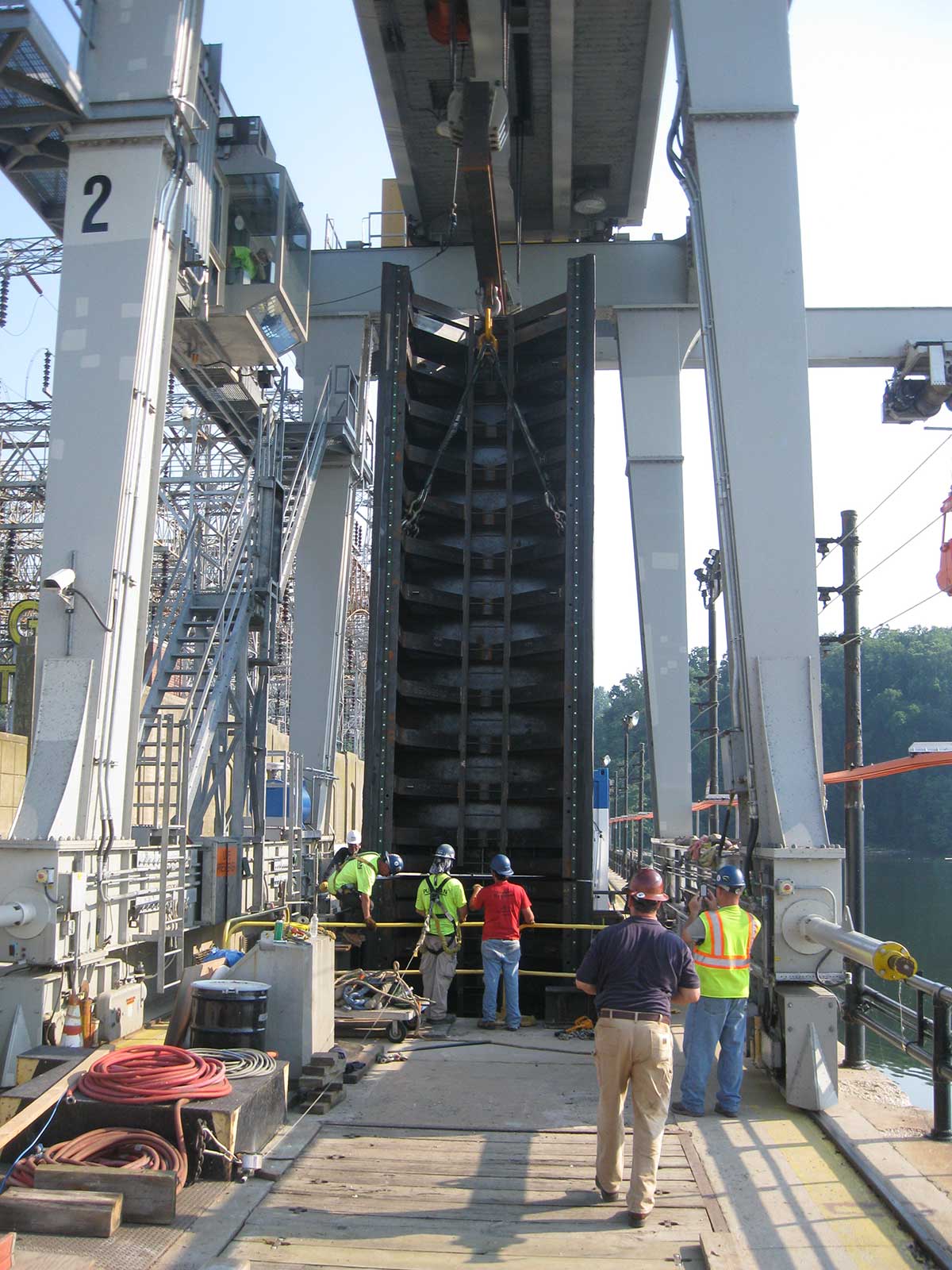
Conowingo Cofferdam
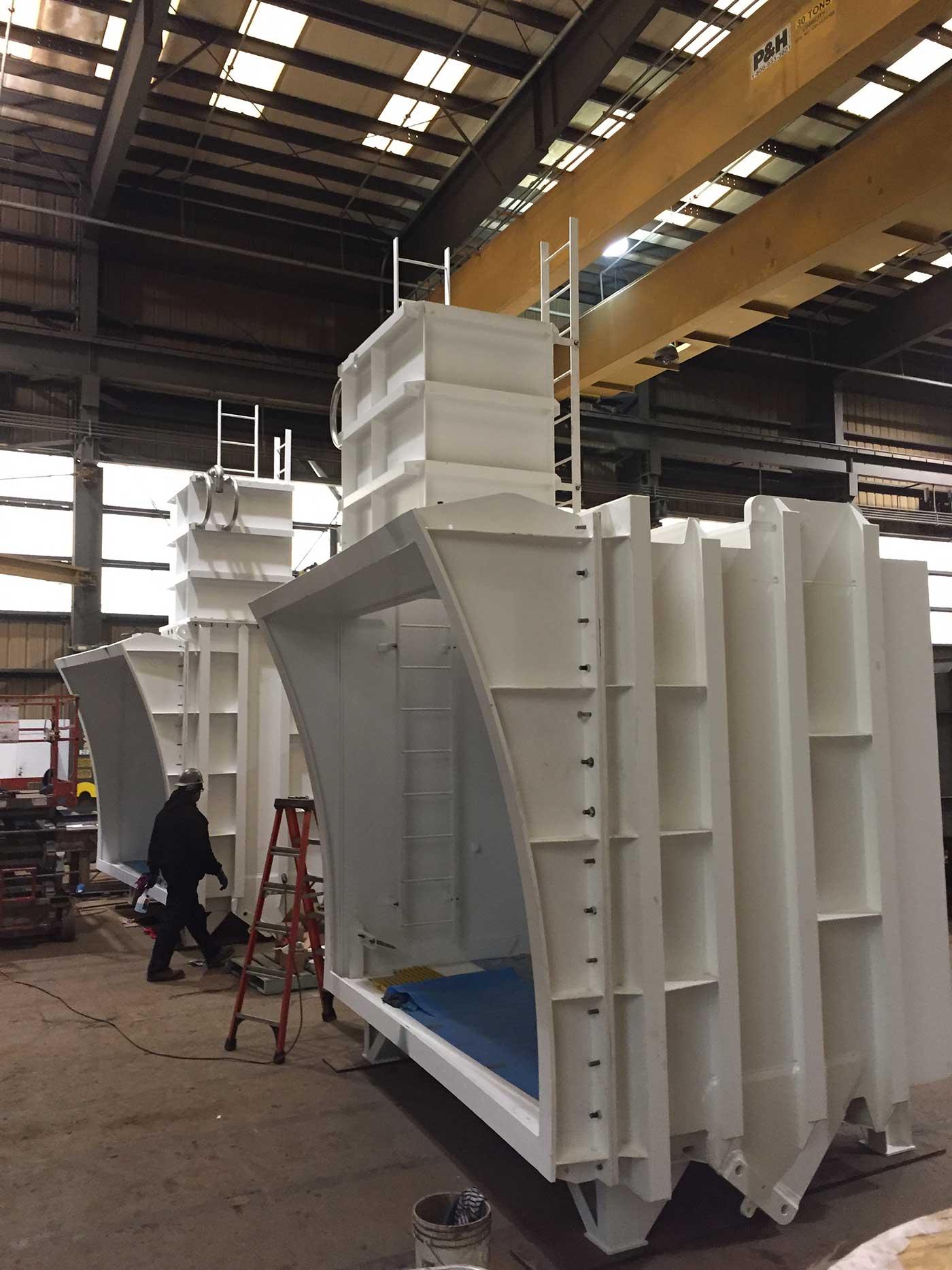
Phoenix Cofferdam
Fabrication of access cofferdams for DDG class vessels.
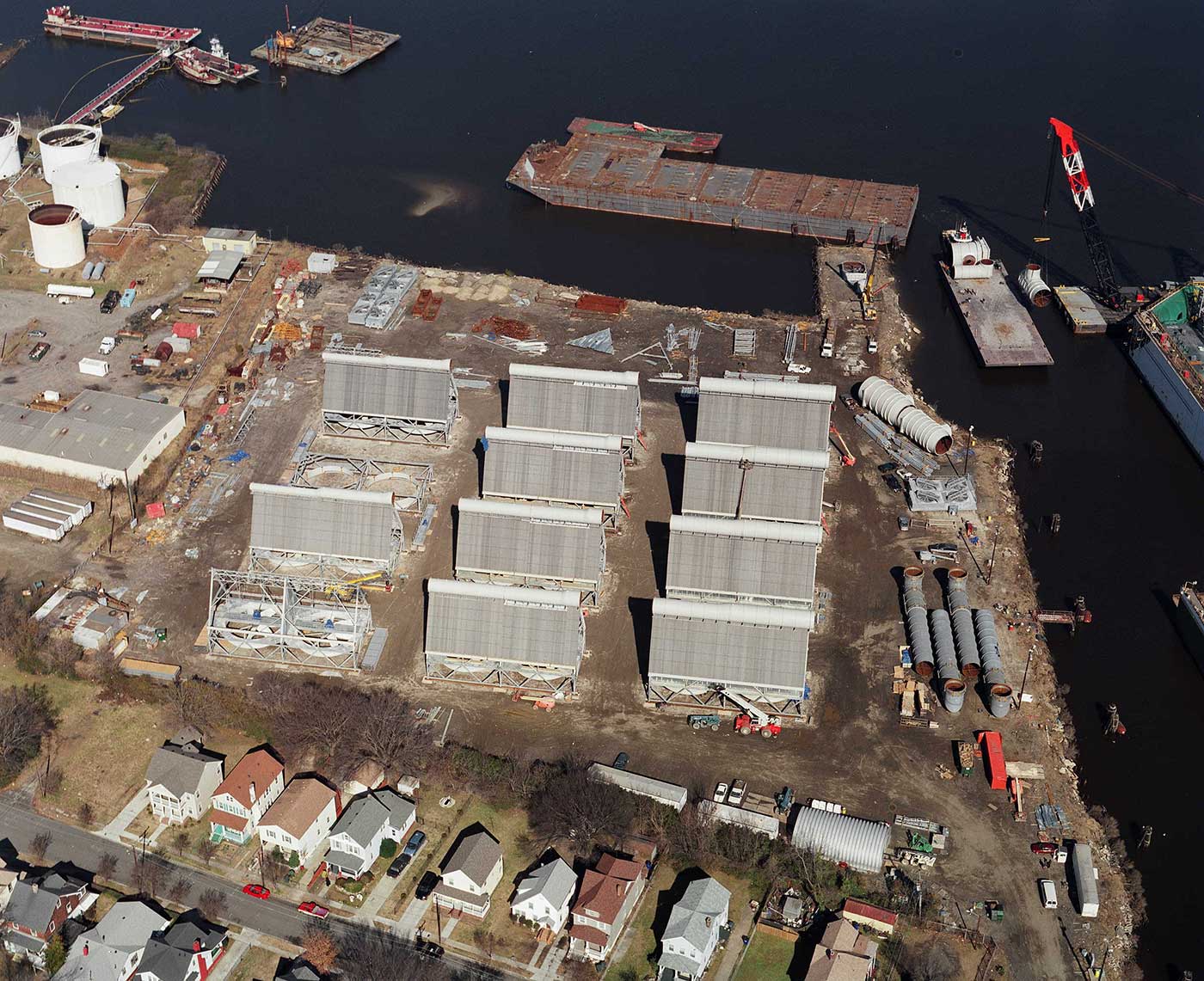
Marley Air Cooled Condensors
This project was to assemble twelve (12) 100’x50’x75’, 285-ton Air Cooled Condensers and delivery the modules via barge to New York City. The project required extensive welding to ASME Title IX and assembly of piping and duct-ing up to 23’ in diameter. Each module employs two (2) 34’ diameter fans. The high degree of modularization adopted in this project was key to the fast con-struction time of the 540 MWe combined cycle plant. Steel America also per-formed complex and technically challenging lifts throughout the project lifecy-cle. This project required 70,000 man-hours expended on a Time and Material contract.
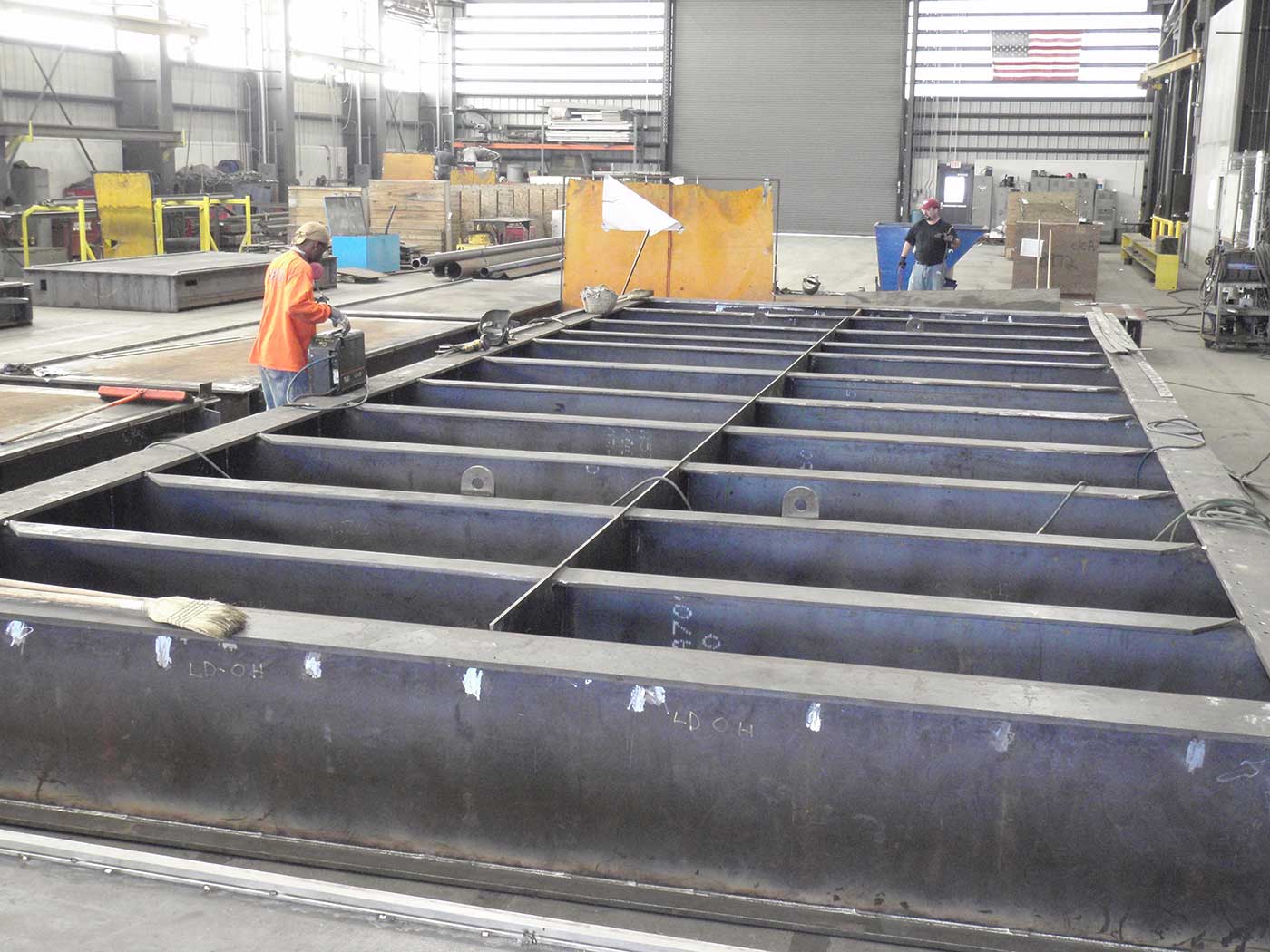
Jefferies Dam Gate
Steel America was contracted to supply fifteen (15) newly constructed stop logs and one (1) newly constructed slide gate for the Jefferies Generating Station. This project included the
detailed design, fabrication, welding, machining, assembly, and painting of the units. The stop logs ranged in size from 6’-7”W x 11’-2”H to 16’-2”W by 22’-0”H with a combined weight of over 103 tons. The slide gate was 16’-9”W x 44’-0”H and weighed approximately 51,000 pounds.
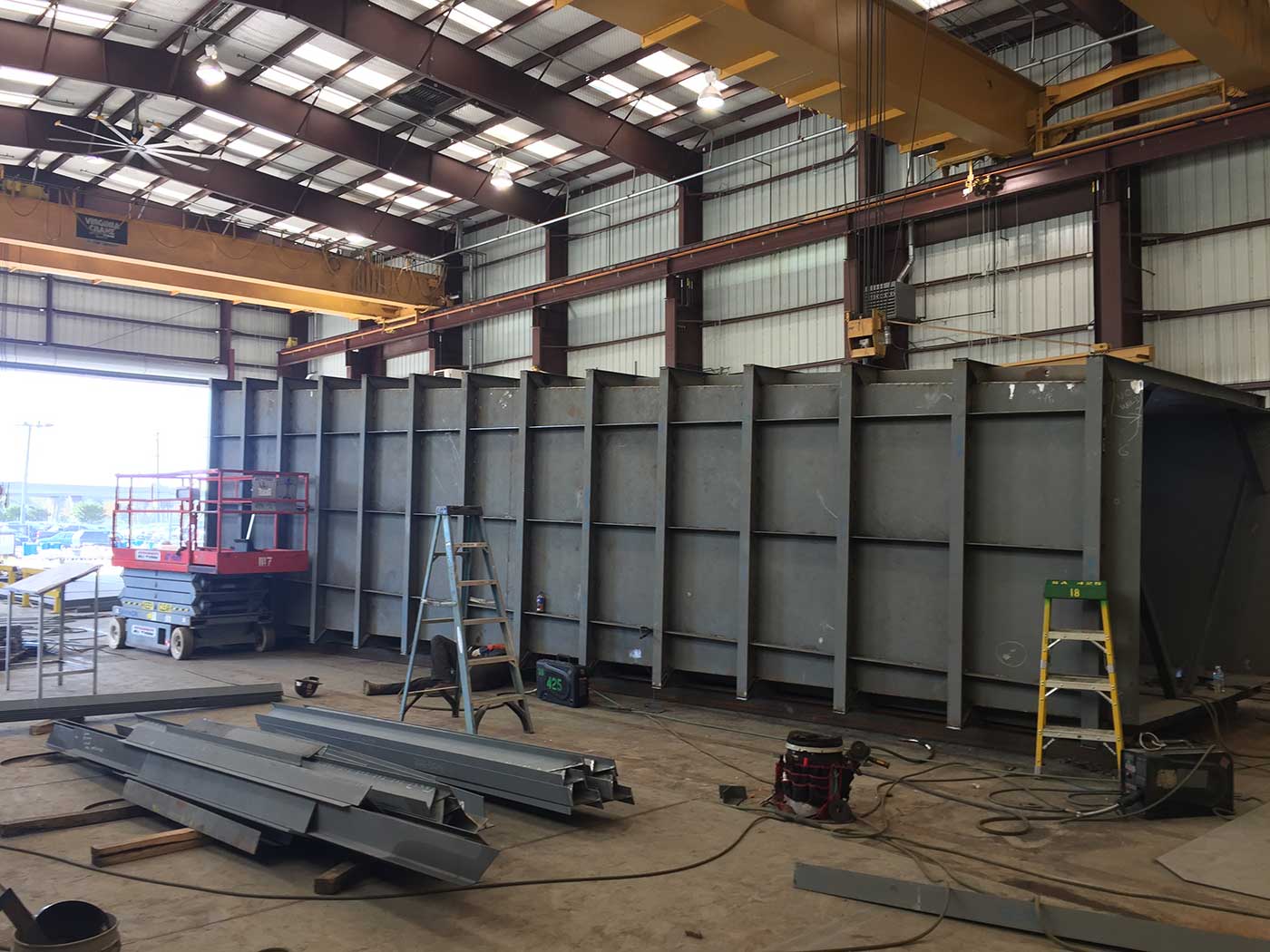
Wind Tunnel
Fabricated a 35’x107’ rectangular wind tunnel, weighing roughly 77-tons, for a leading aeronautical research university. The wind tunnel has two round-to-square transitions throughout the 250’ path of ductwork.
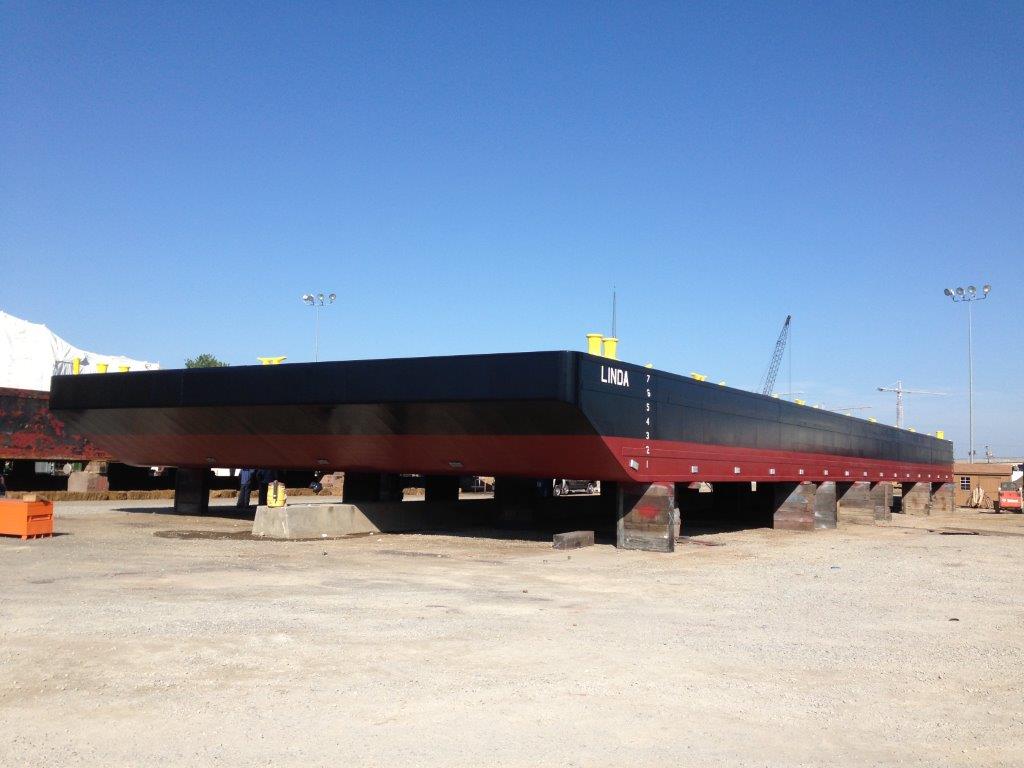
Barge “Linda”
This project required the construction of an ABS Classed, Unrestricted, Oceangoing 160’-0” x 54’-0” x 8’-0” deck barge from modular and panel construction. This barge and kit was the third barge of this type. The barge was transported and launched from Steel America’s West Yard utilizing a 1,000 MT Travelift.
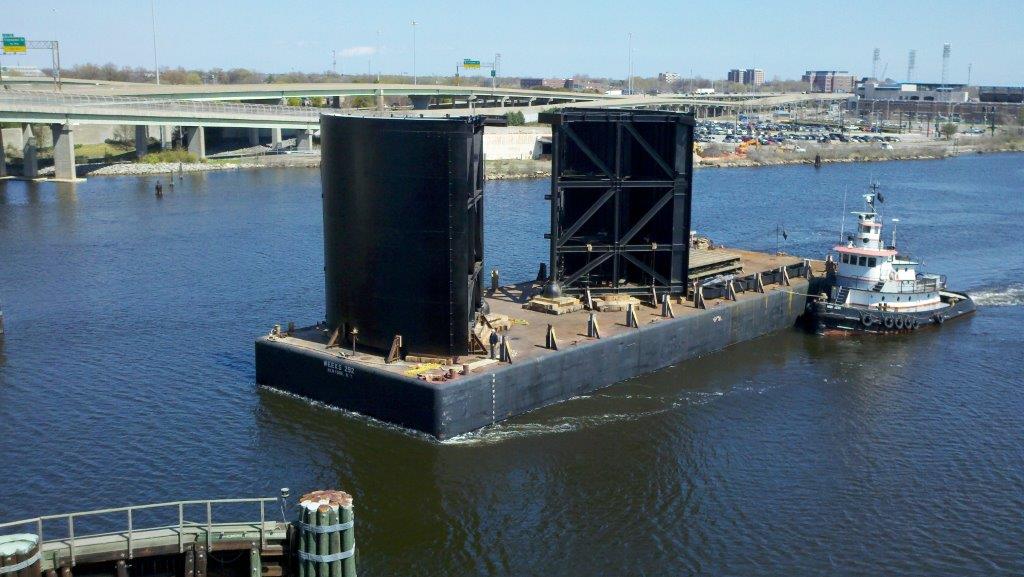
Bayou Dupree Gate
This project is a fabricated two-sided rotating sea traffic and flood control gate that prevents major flooding of waterways and roads near the Mississippi River Gulf Outlet Canal. Each gate section was 33’-0” x 38’-0” x 44’-0”. The gate sections were loaded at Steel America using a 1,000MT Travelift onto an ocean-going barge.
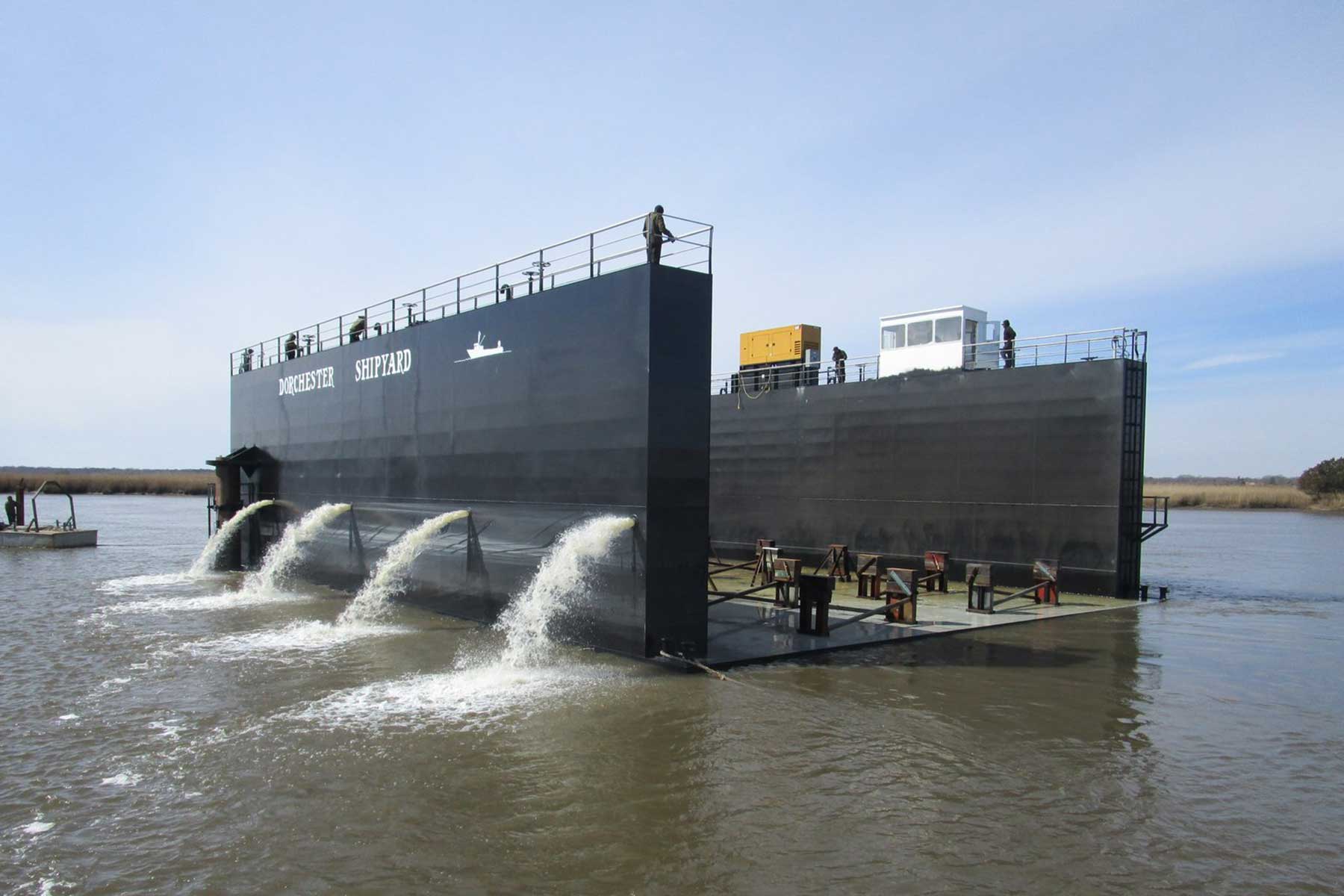
Dorchester Drydock
Steel America was contracted by Dorchester Shipyard to fabricate, assemble, and deliver a 100’ x 71’ floating dry dock. The dry dock was built in 8 modules in the main fabrication shop and transported to the West Yard facility for final assembly using a 1,000-MT Travelift. Upon completion of fabrication and assembly, an on-site team traveled to NJ to complete any final touch-ups and testing.
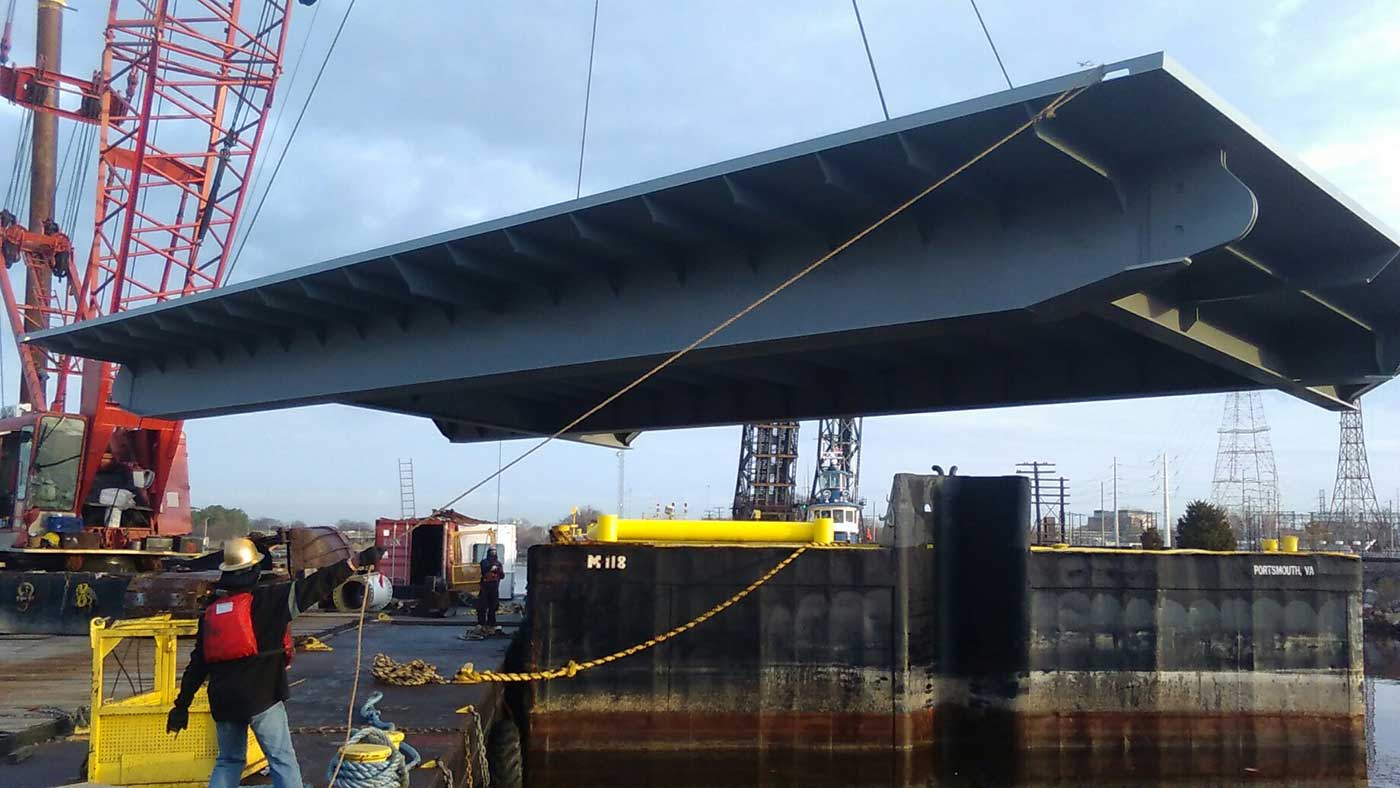
USNS Puller Platforms
Fabrication of Seal Team equipment platform and support structure.
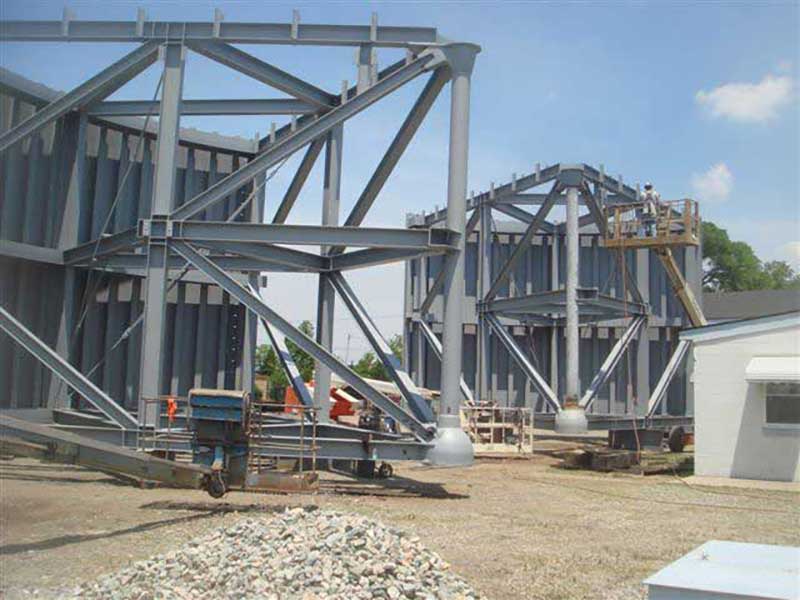
Western Tie-In Gates
The project's fabricated two-sided flood control gate is a critical means of preventing a recurrence of the devastation caused by Hurricane Katrina, by securing the main westerly escape route from New Orleans. Each gate section is 35’-0” x 35’-0” x 26’-0”, and were loaded at Steel America using a 1,000 MT Travelift onto an ocean-going barge. At the site, the customer unloaded the sections using a mobile crane and set them in place. It included five cast iron sluice gates and steel stop logs in addition to numerous other structures. There were approximately 8,000’ of weld and accounted for approximately 10,000 man-hours of labor.
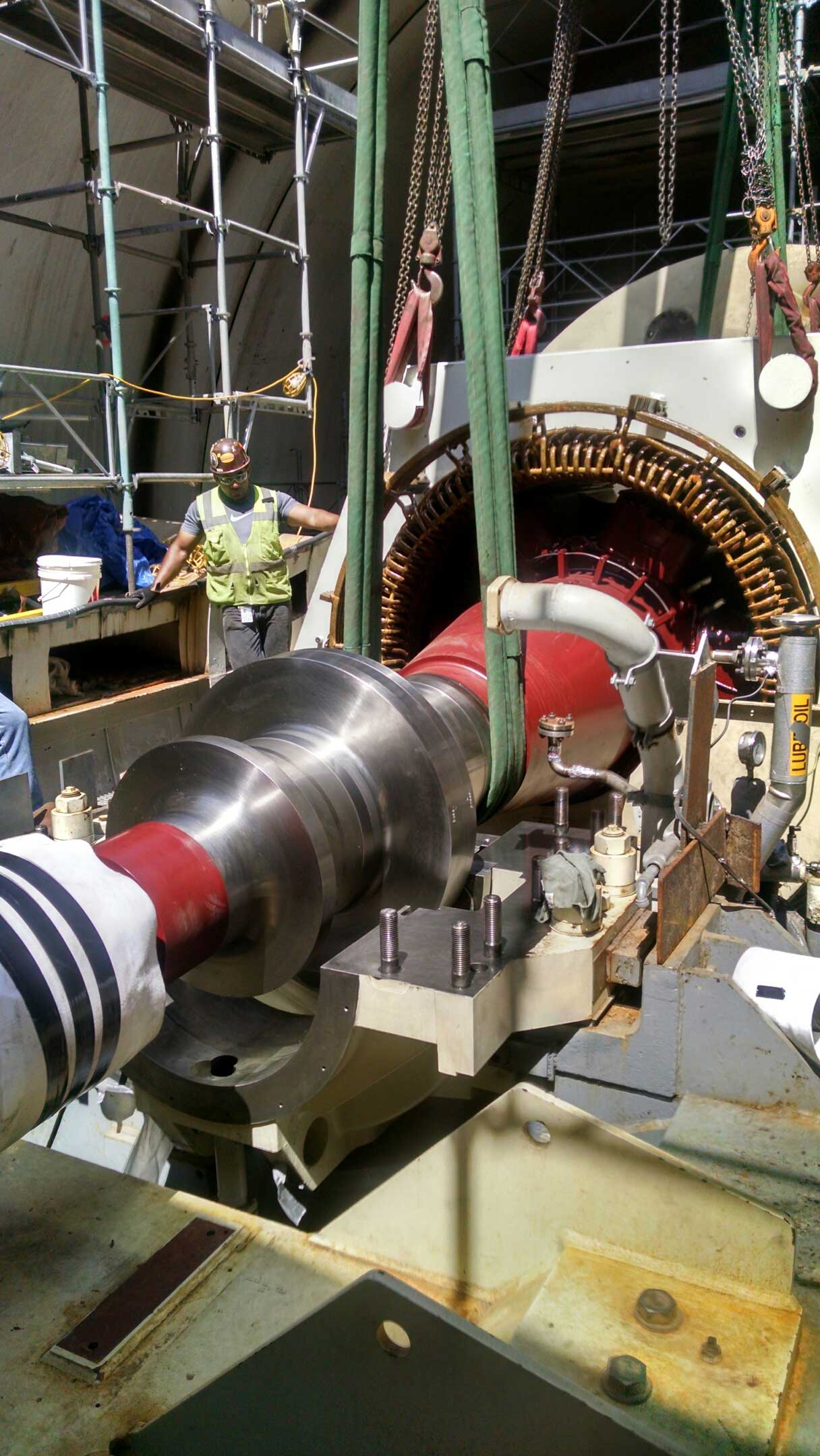
NASA Wind Tunnel
On-site fitting of bearings and seals with the installation of fan assembly.